В настоящий момент изготовление газотурбинных двигателей (ГТД), несмотря на достигнутую высокую степень их технического совершенства, является одной из интенсивно развивающихся отраслей промышленности. На их основе создаются стационарные газотурбинные установки для выработки электроэнергии, приводы для наземного и водного транспорта. Уже сегодня требуется модернизировать и создавать двигатели пятого поколения с повышенными физико-механическими свойствами.
В конструкциях перспективных ГТД военного и гражданского назначения предполагается использование компрессоров низкого (КНД), высокого (КВД) давления и турбин с применением в них блисков, импеллеров и моноколёс. Состояние поверхностного слоя конструкционного материала, применяемого в деталях и сборочных единицах (ДСЕ), представляет собой важный фактор, определяющий эксплуатационные характеристики изделия. Это вызвано тем, что разрушение конструкционного материала детали обычно начинается с её поверхности, а это приводит не только к потере необходимой прочности, но и к ухудшению условий нормальной работоспособности детали.
Упрочнение поверхностного слоя конструкционного материала позволяют решить многие важнейшие технические задачи, но разработка и реализация таких технологических методов упрочнения представляет собой исключительно сложную проблему науки и производства.
Надёжность ГТД и механизмов во многом зависит от усталостной прочности тяжело нагруженных при работе деталей. Усталостные разрушения деталей практически всегда начинаются с поверхностного слоя, где обычно имеется значительное количество различных дефектов. Упрочнение методом поверхностного пластического деформирования является эффективным технологическим способом повышения усталостной прочности деталей.
В мировой практике, при производстве ГТД используются установки для ультразвукового упрочнения деталей. Основным узлом данной установки является колебательная система, состоящая из магнитострикционного или пьезокерамического преобразователя, рабочей камеры, в которую помещается обрабатываемая деталь и стальные шарики. Все ультразвуковые устройства оснащаются надёжной звукоизоляцией.
В процессе ультразвукового упрочнения поверхностный слой подвергается пластической деформации-наклепу. При этом повышается сопротивление деформации и твердость поверхности, изменяется микрогеометрия поверхности, уменьшается количество микроконцентраторов напряжений. Меняется величина и знак остаточных напряжений.
Глубина и степень наклёпа, в значительной степени влияют на прочность деталей. Под степенью наклёпа понимается отношение микротвёрдости поверхностного слоя к микротвёрдости сердцевины, выраженное в процентах.
Существенную роль играет величина и знак остаточных напряжений. В процессе эксплуатации растягивающие напряжения складываются с действующими циклическими растягивающими напряжениями, ускоряется процесс разупрочнения и образования усталостных трещин.
Ультразвуковое упрочнение позволяет улучшить такие эксплуатационные характеристики поверхностного слоя, как опорная поверхность, контактная жёсткость и коэффициент трения скольжения.
К достоинствам ультразвукового упрочнения следует также отнести возможность применения данной технологии для упрочнения поверхностного слоя деталей, имеющие сложнопрофильную геометрию. При этом достигается выгодное распределение внутренних напряжений в металле и такое структурное состояние, при котором удается повысить в два-три раза запас прочности деталей, работающих при переменных нагрузках, и увеличить срок их службы в десятки раз.
Данная статья описывает исследование технологического процесса ультразвукового упрочнения моноколёс и лопаток. А именно исследование величины и глубины залегания остаточных напряжений в поверхностном слое образцов деталей после ультразвукового упрочнения.
Для того чтобы оценить эффективность упрочняющей ультразвуковой обработки шариками проточной части лопаток и моноколес была использована специальная установка «Stressonic», французской марки SONATS. Оценка производилась по критерию остаточных напряжений и был определён следующий порядок исследований:
- Из листа проката материала ВТ-6 толщиной 4мм вырезают фрезерованием пластины размером 200x200мм, из которых в свою очередь электроэрозионным методом вырезают образцы размером 20х4хН четырех типов:
Н = 4мм (прокат), Н = 3–0,1мм, Н = 2–0,1мм, Н = 1,7–0,2мм.
- Образцы всех типов последовательно размещают в гнёздах прямоугольной формы на технологической лопатке и закрепляют в соответствии с технологией.
- Производят обработку в течение установленного времени.
- Обработанные образцы исследуют на распределение остаточных напряжений.
- Результаты анализируют, устанавливают закономерность распределения напряжений по сечениям лопаток различной толщины.
- На упрочнённом моноколесе проводятся усталостные испытания.
- Анализируются результаты усталостных испытаний моноколеса.
- По результатам усталостных испытаний и результатам определения распределения остаточных напряжений принимается решение об эффективности технологии ультразвукового упрочнения моноколёс.
Для гарантии надёжности изделия, при разработке конструкторской и технологической документации, при обеспечении технологических процессов необходимо учитывать и контролировать такие параметры качества, как шероховатость, наклёп и остаточные напряжения в поверхностном слое детали. Требования к качеству поверхности деталей подлежат проверке при сертификации производства.
Центральный институт авиационного моторостроения (ЦИАМ) разработал «Руководство по нормированию остаточных напряжений в поверхностных слоях» опытных и серийных деталей ГТД. Устанавливаемые нормы регламентируют:
величину максимальных напряжений сжатия в поверхностном слое;
глубину распространения сжимающих напряжений;
величину максимальных подслойных растягивающих напряжений.
ЦИАМ регламентирует методику определения, проведение контроля, оценку результатов контроля и назначение норм на остаточные напряжения для деталей двигателей.
В «Руководстве» приводятся формулы статистической обработки результатов измерений остаточных напряжений с целью выявления среднего значения нормируемой величины и её допустимого отклонения. Также приводятся рекомендуемые нормы на параметры остаточных напряжений в лопатках турбин и компрессоров.
Механическим методом по Давиденкову определяют напряжения 1-го рода. Механический метод определения остаточных напряжений основан на вырезке из детали образца и послойном удалении исследуемых слоев путём электрохимического травления. При этом происходит нарушение равновесия, в результате чего образец деформируется. По величине изменения деформации оставшейся части образца, с изменением глубины залегания исследуемых слоёв, рассчитывают остаточные напряжения.
В основу расчётов остаточных напряжений положен принцип обратных напряжений, поскольку измеряется деформация образца, возникающая как результирующая составляющая сил, действующих вдоль вновь образовавшихся поверхностных слоёв в результате электрохимического стравливания исследуемых слоёв. Процесс травления подобран таким образом, что не создаёт побочной деформации образца.
Механический метод получил наибольшее распространение не только из-за своей простоты, но и вследствие того, что он использует представления о напряжениях и деформациях механики твёрдого тела как при расчётах деталей на прочность, жёсткость и устойчивость.
При механической обработке детали остаточные напряжения в разных направлениях могут отличаться не только по величине, но и по знаку. При дробеструйных методах упрочнения и виброобработке остаточные напряжения в разных направлениях одинаковы, если снята наследственность предыдущих операций.
Обычно определяют распределение остаточных напряжений по глубине залегания исследуемых слоев вдоль главных направлений, совпадающих с направлением действия рабочих нагрузок или с направлением обработки поверхности.
Наиболее простыми являются измерения в призматических образцах, в предположении об одноосном напряжённом состоянии образца.
В случае потребности определения плоского напряжённого состояния, необходимо вырезать на плоскости три образца под углом 45°. Вырезка образцов не должна вносить изменения в поверхностное напряжённое состояние, подлежащее исследованию. Вырезку образцов необходимо производить электроэрозионным методом проволокой на «мягких» режимах.
Не допускается в процессе изготовления образцов применять воздействия, способные нарушить собственное напряжённое состояние образца: дорабатывать напильником, гнуть, наносить царапины и вмятины на исследуемую поверхность.
Процесс ультразвукового упрочнения моноколес на базе специальной установки «Stressonic», французской марки SONATS, представляет следующую последовательность:
1. Моноколесо помещается в ультразвуковую камеру;
2. В ультразвуковую камеру помещается необходимое для обработки количество дроби;
3. Закрывается верхний колпак;
4. Включается программа обработки моноколеса на ЭВМ установки;
5. По завершении цикла обработки установка в автономном режиме завершает процесс упрочнения;
6. Открывается верхний колпак;
7. Из ультразвуковой камеры извлекается дробь;
8. Моноколесо извлекается из ультразвуковой камеры.
Рис. 1. Схема установки моноколеса в ультразвуковой камере
Режим обработки моноколеса представлен в следующей последовательности:
1. Управляющая программа обработки — «Big Blisk»;
2. Номинальная частота генератора — 20кГц;
3. Давление воздуха в сети Р= 40–45мПа (4–4,5кгс/см2);
4. Частота вращения детали — 0,50,2об/мин;
5. Время обработки детали — 11 часов;
6. Диаметр и материал микрошариков — 1,5мм из стали 100С6 аналогШХ15 (ГОСТ 3722–81);
7. Масса шариков — 1700,1гр;
8. Срок службы микрошариков — 110 часов.
По окончании обработки производится визуальный осмотр обработанных поверхностей на предмет оценки сплошности покрытия и равномерности упрочняющей обработки. Не допускается:
наличие неупрочнённых зон в местах подлежающих упрочнению;
наличие рисок, забоин и следов постороннего механического воздействия на поверхности детали, после упрочнения.
Для оценки глубины и степени наклёпа, а также структуры и глубины изменённого в результате ультразвукового упрочнения поверхностного слоя в металлографической лаборатории проводились исследования на четырёх образцах из сплава ВТ-6.
При внешнем осмотре упрочнённых поверхностей всех четырёх образцов видно, что поверхность на образце № 1 с более грубым рельефом, чем у трёх остальных (Рис. 2).
Рис. 2. Внешний вид всех упрочненных поверхностей
Исследованием микрошлифов изготовленных в поперечном сечении установлено:
микроструктура материала всех четырёх образцов соответствует 3–4-му типу 9–ти типной шкалы микроструктур титановых сплавов.
Рис. 3. Характерная микроструктура образцов
макроструктура материала всех четырех образцов соответствует 4–5 баллу 10-ти бальной шкалы макроструктур титановых сплавов, на смешанном фоне;
на поверхности образцов и в сердцевине различия в микроструктуре не наблюдается.
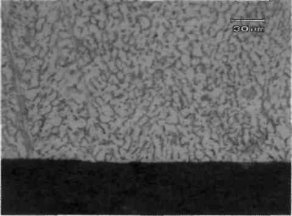
Рис. 4. Характерная микроструктура на поверхности образцов
Результаты замеров микротвёрдости, которые производились непосредственно на поверхности, подвергаемой ультразвуковому упрочнению, и в сердцевине образцов, приведены в таблице 1.
Таблица 1
№ образца |
Микротвердость, HV кгс\мм2 |
Степень наклепа, % |
||
Поверхность |
Сердцевина |
На гл. ~0,02мм |
||
1 |
393 |
351 |
352 |
12 |
2 |
383 |
331 |
334 |
15 |
3 |
386 |
346 |
346 |
11 |
4 |
387 |
361 |
361 |
7 |
Для определения остаточных напряжений проводились исследования на комплексе МерКулОн «Тензор-3".
Рис. 5.
Рис. 6.
На графиках Рис. 5 и Рис. 6, приведены эпюры остаточных напряжений на трёх образцах пластин 3 и 4 соответственно. На глубине более 5мкм наблюдается хорошая воспроизводимость результатов. Рассчитана средняя эпюра остаточных напряжений.
На глубине менее 5мкм большое влияние на процесс травления оказывает нестабильность окисленного слоя на поверхность титана, который является запорным слоем для прохождения электрического тока в момент его включения при определении остаточных напряжений.
Рис. 7.
На Рис. 7 показаны усредненные эпюры остаточных напряжений для всех четырёх пластин.
Усталостным испытаниям подвергались 6 лопаток, изготовленные в следующей последовательности:
фрезеровка-ручная полировка;
виброполировка на установке «Rosler»;
ультразвуковое упрочнение на специальной установке «Stressonic», французской марки SONATS.
Испытания проводились при изгибных колебаниях по основному тону с симметричным циклом нагружения в условиях комнатной температуры по режиму:
напряжение в наиболее напряжённом месте профиля пера лопаток σн=37кгс/мм2;
база N =2107 циклов.
Для испытаний лопатки препарировались тензорезисторами с базой 3мм. Уровень напряжения при испытании задавался по тензорезистору, фиксирующему больший уровень напряжений.
В таблице 2 приведены параметры нагружения лопаток при усталостных испытаниях.
Таблица 2
№ № п/п лопатки |
к (кгс/мм2) |
Ат.л. вх.кр. (мм) |
f1.0 (Гц) |
№ (циклы)106 |
|
Начало |
Конец |
||||
1 |
37 |
16,50 |
289 |
289 |
20,0 |
2 |
37 |
16,28 |
286 |
286 |
20,0 |
3 |
37 |
16,35 |
288 |
288 |
20,0 |
4 |
37 |
16,80 |
288 |
288 |
20,0 |
5 |
37 |
16,70 |
289 |
289 |
20,0 |
6 |
37 |
17,24 |
289 |
289 |
20,0 |
Результаты металлографических исследований, проведённых на четырёх образцах из сплава ВТ-6 показали:
Глубина упрочненного поверхностного слоя на всех четырёх образцах не более 0,02 мм, со степенью наклёпа 7–15 %.
Каких-либо структурных изменений на поверхности в месте упрочнения не наблюдается.
По результатам исследования остаточных напряжений можно судить об упрочнении поверхностного слоя на глубину до 100мкм.
Усталостные испытания лопаток моноколеса выдержали заданный режим испытаний без признаков разрушений.
Проведенные испытания и исследования показали, что технология ультразвукового упрочнения на базе специальной установки «Stressonic», французской марки SONATS удовлетворяет техническим требованиям производства моноколеса.
Очевидно, что использование технологии ультразвукового упрочнения при создании ДСЕ двигателей 5-го поколения станет неотъемлемой частью технологического процесса их изготовления. Также в серийных ГТД для повышения экономической эффективности их использования необходимо проводить мероприятия по увеличению назначенного ресурса основным деталям и увеличения времени межремонтного ресурса. Внедрение технологии по упрочнению поверхностей основных деталей ГТД положительным образом отразится на их надежности, тем самым позволит решить данные задачи.
Литература:
- Пат. 2340867 РФ, МПК G 01B 7/16 Способ определения остаточных напряжений в деталях с электропроводными покрытиями и устройство для его осуществления / Меркулова Н. С., Гринченко М. И., Иванова Т. О. Федеральное государственное унитарное предприятие «Московское машиностроительное производственное предприятие «Салют» (РФ) — Опубл.10.12.2008 г.
- Подзей А. В., Сулима А. М., Евстигнеев М. И. Технологические остаточные напряжения. Под редакцией А. В. Подзея. М. Машиностроение. 1973г. 216 с.
- Кузнецов Н. Д., Цейтлин В. И., Волков В. И. Технологические методы повышения надежности деталей машин (справочник) // М. Машиностроение, 1993г, С.161–162).