Применение железомарганцевых руд Центрального Казахстана для выплавки стандартных марганцевых ферросплавов по действующим технологиям невозможно из-за низкого содержания марганца и высокого содержания железа. Поэтому сотрудниками Химико-металлургического института, разрабатывается новый метод обжигмагнитной переработки железомарганцевых руд, включающий стадию низкотемпературного восстановления железа газовыми углями месторождения Шубарколь и последующую магнитную сепарацию, позволяющую отделить восстановленное до ферромагнитной формы железа от марганцевой части рудного сырья[1-2].
В качестве топлива и восстановителя в обжиговых печах, зачастую при обжиге железомарганцевых руд используется бурый уголь с повышенным содержанием не только летучих, но и влаги. В случае использования в качестве обжигового агрегата шахтные печи, необходимо учитывать, что шахтные печи камерного типа внешнего нагрева имеют один серьезный дефект – они конденсируют, то есть выделяют из трубы черную жидкость со специфическим запахом.
Когда, температура отходящих газов низка или стенки дымовой трубы сильно охлаждены, то все водяные пары, охлаждаясь в трубе, оседают на ее стенках в виде капель воды, смешиваются с несгоревшими частицами топлива и начинают стекать по трубе, пропитывая при этом кирпич. Увлажненные стенки трубы сыреют, что ухудшает тягу в трубе и постепенно разрушает кирпич, образуя на поверхности пятна. Поэтому при магнетизирующем обжиге железомарганцевых руд не желательно применять бурые угли, содержащие повышенное количество гигроскопической и гидратной влаги.
В результате испытаний по обжигу железомарганцевых руд наилучшие результаты по магнетизирующему обжигу получены при использовании низкозольного шубаркольского угля [3].
Шубаркольский уголь, добываемый открытым способом, отличающийся низкой влажностью и невысокой зольностью (в среднем около 6%, а в отдельных пачках – и до 2-3%), наиболее подходит для обжиговых процессов. Весьма благоприятным показателем качества угля является и небольшое содержание фосфора (порядка 0,01%).
Классификация шубаркольского угля связана с определенными трудностями, так как этот уголь обладает признаками, одни из которых, по существующим представлениям, характерны для буроугольной стадии углефикации, а другие – для каменных длиннопламенных углей. К последним шубаркольский уголь может быть отнесен, исходя из высокой теплоты сгорания (более 30 МДж/кг), высокого содержания витринита (85%) и низкой зольности. В то же время, оценивая возможности хранения, транспортировки и переработки этого угля, следует учитывать, что он не вполне «дозрел» до типичного каменного угля, вследствие чего должен неизбежно характеризоваться невысокой прочностью. Действительно, как показали исследования, выполненные в Кузнецком центре ВУХИН, шубаркольский уголь характеризуется низкими показателями структурной прочности (55,9%) и термической стойкости (58,1%).
При обжиге железомарганцевых руд в шахтной печи камерного типа внешнего нагрева использование избыточного количества низкозольного шубаркольского угля не только делает возможным селективное разделение железа и марганца, но и позволяет получить в обожженной руде коксовый остаток – полукокс [1].
Физико-химические характеристики восстановителя влияют как на показатели обжига и работу обжиговой печи, так и на качество конечной продукции. Поэтому зольность применяемого в качестве восстановителя – шубаркольского угля, влияет на зольность полукокса получаемого в результате восстановительного обжига.
С целью изучения удельного электрического сопротивления (УЭС) полукокса, получаемого при обжиге, специалистами лаборатории пирометаллургических процессов была собрана и испытана установка для измерения УЭС углеродистых материалов(рисунок 1). Основным условием было сохранение сущности метода измерения падения напряжения на участке столбика углеродистого материала с крупностью зерен 0,315-
0,400 мм, заключенного в матрице между двумя пуансонами под давлением (5,88+-0,03) МПа[(60,0+-0,3) кгс/см2] при прохождении постоянного тока. ГОСТ 4668-75 [3-5].
Конструктивно установка (рис. 1) представляет собой станину с прямоугольной распорной аркой, на которой установлены весы напольные, домкрат и матрица.Весы напольные диапазон 0-120 кг (для измерения давления). Домкрат позволяет плавно и без усилий создавать давление до 60 кг на 1 см2. Матрица изготовлена по чертежам ГОСТ 4668-75 (рис. 2). Источник стабилизированного постоянного тока 0,5А.





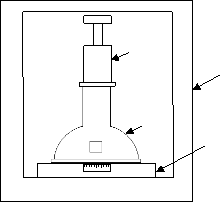
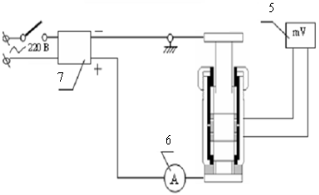
1 – прямоугольная распорная арка; 2 – весы напольные; 3 – домкрат; 4 – матрица; 5 – милливольтметр; 6 – амперметр; 7 – источник тока
а – установка для измерения УЭС; б – схема измерительной цепи
Рис. 1.Принципиальная схема
1,7 – токовые зонды; 2,4,6 – изоляционные втулки; 3,5 – пот.зонды; 8 – изол. шайба;
9 – изоляционная втулка; 10 – гайка и корпус; 11 – пуансоны; 12 – в сборе
Рис. 2. Матрица для измерения УЭС (ГОСТ 4668-75)
Для проведения испытаний используют блок питания, работающий в двух режимах: источник постоянного тока, поддерживающий ток 0,5A (рекомендованного ГОСТ 4668-75), используется для измерения с удельным сопротивлением материала до 1 МОм*м. Второй режим – это источник постоянного напряжения для измерения более высокого сопротивления. Использованный блок питания упрощает процедуру измерения и расчетов, защищен от высоких токов. Для юстировки имеется «Точная настройка».
Собранная установка позволяет определять УЭС углеродистых материалов по ГОСТ 4668-75, но также определить зависимость изменения УЭС от прикладываемого давления. В таблице 1 приведены значения УЭС полукоксов, полученных при восстановительном обжиге [1], а также углеродистых восстановителей применяемых в настоящее время на ферросплавных заводах. Также для примера приведены значения УЭС у графита.
Таблица 1
Результаты определения УЭС у различных углеродистых материалов в зависимости от давления
Материал |
Давление, кг |
Напряжение, V |
Сила тока, А |
УЭС, Ом*м |
УЭС, 10-6 Ом*м |
120/60 |
Полукокс №1 |
60 |
12,1 |
0,000098 |
3102 |
3101551020 |
127,1 |
120 |
20,2 |
0,000208 |
2440 |
2439538462 |
100,0 |
|
Полукокс №2 |
60 |
9,8 |
0,000022 |
11190 |
11189818182 |
132,0 |
120 |
13,5 |
0,00004 |
8478 |
8478000000 |
100,0 |
|
Полукокс №3 |
60 |
16,7 |
0,000088 |
4767 |
4767090909 |
131,2 |
120 |
18,8 |
0,00013 |
3633 |
3632738462 |
100,0 |
|
Графит |
60 |
0,0088 |
0,5 |
0 |
442 |
160,0 |
120 |
0,0055 |
0,5 |
0 |
276 |
100,0 |
|
Кокс КНР |
60 |
0,228 |
0,5 |
1 |
912000 |
271,4 |
120 |
0,084 |
0,5 |
0 |
336000 |
100,0 |
|
Спецкокс ТОО "Сарыарка Спецкокс" |
60 |
0,874 |
0,5 |
3 |
3496000 |
260,1 |
120 |
0,336 |
0,5 |
1 |
1344000 |
100,0 |
|
Спецкокс ТОО "Сарыарка Спецкокс" |
60 |
0,893 |
0,5 |
4 |
3572000 |
229,0 |
120 |
0,39 |
0,5 |
2 |
1560000 |
100,0 |
Проведенные исследования показали, что УЭС полученного полукокса на 3-4 порядка (в 1000 и 10000 раз) выше, чем у углеродистых восстановителей, применяемых в настоящее время на ферросплавных заводах (кокс КНР и спецкокс ТОО "Сарыарка Спецкокс").
Повышенное удельное электросопротивление углеродистых восстановителей при рудно-термической плавке значительно улучшает технико-экономические параметры выплавки ферросплавов, за счет более глубокой посадки электродов, увеличения снимаемой мощности печи и температуры процесса. Как видно из таблицы 2, полученный полукокс соответствует основным требованиям стандартов производства полукокса.
Таблица 2
Характеристики полукокса
Показатель |
Требования |
Полученный полукокс |
Комментарий |
Теплота сгорания на рабочую массу, ккал/кг |
Не менее 6000 |
6500-7200 |
Изменяя режимные параметры, можно увеличить выход полукокса, снизив его калорийность до 6000-6500 ккал/кг. |
Зольность на рабочую массу. % |
Не выше 15 |
7-8 |
Незначительно зависит от режимных параметров и существенно от зольности исходного сырья. |
Выход летучих веществ, % |
Не выше 12 |
5-15 |
Зависит от режимных параметров. Можно получать полукокс с выходом летучих веществ более 15%. |
Влажность, % |
2-12 |
0-6 |
Сухой метод сушения |
Таким образом, применение в магнетизирующем обжиге железомарганцевых руд низкозольного Шубаркольского угля положительно влияет на работу печи, на показатели обжига и полученный после обжига совместный продукт – полукокс соответствует основным требованиям стандартов производства полукокса, а также обладает лучшим специфическим свойством.
Литература:
- Разработка технологии обжигмагнитного обогащения железомарганцевых руд Казахстана: отчет о НИР /ХМИ им. Ж. Абишева. – Караганда, 2012. – С. 8-40.
- АбилбериковаА.А., БайсановА.С., ТорговецА.К, СамуратовЕ.К. Экспериментальная установка для обжига железомарганцевых руд // Материалы Республиканского научного журнала «Технология производства металлов и вторичных материалов». – Темиртау, 2013.
- Абилберикова А.А., Байсанов А.С., Самуратов Е.К., Оспанов Н.И., Абилбериков А.А. Обжиг железомарганцевых руд Казахстана в камерной печи внешнего нагрева //Мат. Междун. научно-практ. конф., посв. 20-летию РГП «НЦ КПМС РК» и 55-летию Химико-металлургического института им.Ж.Абишева «Проблемы и перспективы развития горно-металлургической отрасли: теория и практика». – Караганда, 2013. – С.71-74.
- Жучков В.И., Микулинский А.С. Методика опреления электрического сопротивления кусковых материалов и шихт // Экспериментальная техника и методы высокотемпературных измерений. – М.: Наука, 1966. – С.43-46.
- Павлинский Н. И., Ганцеровский О. Г. Электросопротивление шихт для выплавки углеродистого ферромарганца // Металлургия и коксохимия, 1974. – С.84-86.