В статье рассматривается краткий обзор литератур, посвященные к физическим основам очистки поверхности кремния и арсенид галлия, от технологических примесей. Анализ классических зарубежных литератур показывало, что после нескольких лазерных импульсов происходит дальнейшее улучшение чистоты поверхности и совершенства кристаллической структуры поверхностного слоя этих материалов.
Ключевые слова: лазер, поверхность, углерод, кислород, электронная оже-спектроскопия
Современная электроника, включая производство полупроводниковых материалов и микроэлектронных приборов, имеет дело только со сверхчистыми материалами, а также сверхчистыми (вакуумными) условиями получения полупроводниковых материалов и приборов на их основе. В полупроводниковых и микроэлектронных технологиях одной из основных операций процесса производства является очистка поверхностей полупроводниковых материалов от технологических примесей [1, 2].
В последние годы развивается перспективный метод очистки поверхности с помощью импульсного лазерного облучения. Для получения чистой и совершенной поверхности уникальные возможности представляет импульсное лазерное облучение, которое обеспечивает стерильность процесса очистки и получения совершенной кристаллической структуры активного поверхностного слоя наиболее используемых полупровниковых материалов.
Этот метод наиболее изучен применительно к кремнию и арсенид галлию [3]. Поэтому сначала обратим внимание к основным результатам по влиянию импульсно-лазерного воздействия на поверхностных свойств этих материалов.
Предварительный анализ (до лазерного облучения) состава поверхностного слоя пластин кремния, вырезанных вдоль плоскости (100) или (111), методом обратного резерфордовского рассеяния показал, что поверхностная концентрация атомов кислорода и углерода составляет 8,1·1015 и 3,5·1015 см-2, т. е. помимо углеродной пленки на поверхности кремния имеется слой SiO2 толщиной около 2 нм. Исследования проводились в высоковакуумной установке. Лазерное излучение вводилось внутрь установки через стеклянное окно. В качестве источника излучение использовался рубиновый лазер, работающий в одномодовом режиме и обеспечивающий плотность потока энергии в пределах 0,2–4,0 Дж/см2. Длительность импульса сохранялась постоянной 150 нс, а диаметр лазерного пучка был около 3,5 мм. Измерения состава поверхности после облучения производились методом оже-электронной спектроскопии.
Об изменении элементного состава поверхности свидетельствовало изменение амплитуды оже-пиков кислорода (509 эВ), углерода (272 эВ) и элемента подложки на спектрах с поверхности кремния и арсенида галлия и их отношения к амплитудам пиков основного материала образцов — кремния (92 эВ) (рис. 1.) и мышьяка (31 эВ) (рис. 2.)
Облучение образца одним лазерным импульсом (~ 2 Дж/см2) вызывает снижение интенсивности углеродных (1 линия, рис. 1.) и кислородных (2 линия, рис. 1.) сигналов. После облучения пятью лазерными импульсами интенсивности О- и С-сигналов оказываются на уровне фона. После пятнадцати лазерных импульсов происходит дальнейшее улучшение чистоты поверхности и совершенства кристаллической структуры поверхностного слоя. Количество находящегося на поверхности кислорода и углерода не превышает 0,001 от монослоя.
Рис. 1. Зависимость отношений амплитуд пиков С/Si (1) и O/Si (2) от числа световых импульсов nu [3]
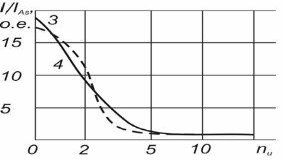
Рис. 2. Зависимость отношений амплитуд пиков С/As (1) и O/As (2) от числа световых импульсов nu [3]
На рис. 3 представлена зависимость отношения амплитуды оже-пиков кислорода и углерода поверхности (100) образцов кремния к амплитуде пика кремния от плотности энергии в лазерном пучке при облучении 15 импульсами. По характеру этой зависимости можно судить, что лазерно-стимулированная десорбция углерода и кислорода с поверхности кремния имеет пороговый характер и начинается при 1 Дж/см2.Эффективность очистки постепенно возрастает по мере увеличения плотности энергии в импульсах и ограничивается разрушением поверхности кристалла при средней удельной энергии пучка, превышающей 2,3 Дж/см2 для данного распределения ее по сечению.
Рис. 3. Зависимость отношения амплитуды оже-пиков кислорода и углерода поверхности (100) образцов кремния к амплитуде пика кремния от плотности энергии в лазерном пучке при облучении 15 импульсами [3]
Десорбция примесей, индуцированная лазерным воздействием, наблюдалась в Si и GaAs. Источниками импульсного излучения являются лазеры с модулированной добротностью (λ = 0,694 мкм для рубина и λ = 1,06 мкм для Nd: YAG) с длительностью импульса 20–50 нс и пиковой мощностью около 100 МW/см2. Для соединений типа А3В5 лазерная очистка сопровождается изменением стехиометрического состава поверхности из-за испарения более летучих компонентов. Предполагается, что в процессе лазерной очистки происходит быстрое плавление и затвердевание за время 1 мкс, в течение которого летучие примеси (водород, кислород и др.) испаряются, а другие примеси (например, углерод, металлы) диффундируют через жидкий слой. Оба механизма испарение и диффузия влияют на распределение данной примеси, а относительная роль каждого из механизмов определяется экспериментальными условиями. Диффузия, естественно, зависит от химической природы примеси. Например, бор или мышьяк, имплантированные в кремнии, диффундируют через расплавленный поверхностный слой достаточно равномерно, тогда как имплантированные ионы меди проявляют сегрегацию вблизи поверхности. Установлено, что захват и сегрегация зависят от скорости движения границы раздела жидкость-твердая фаза [4].
Эффекты лазерного воздействия на кремний, а также на оксиды (SiO2, TiO2) кото-рые широко используются в оптических компонентах (окна, покрытия, диэлектрические рефлекторы и др.) мощных лазерных систем, рассмотрены в работе [5].
В конце статьи хотели бы отметить, что импульсно-лазерное очистка поверхности используется, в основном, при производстве полупроводниковых микросхем и имеет ряд существенных преимуществ:
– в обрабатываемую поверхность не вводятся нежелательные технологические примеси (углерод и кислород) [6];
– очистка, может быть, произойти параллельно последующими технологическими процессами [7];
– без воздействия лазерных импульсов на близлежащие участки материала (локальность обработки) [8];
– возможность проведения в едином цикле технологического процесса, различных видов очистки [7].
Литература:
- Мадаминов Х. М., Каримова Г. Применение лазеров в полупроводниковой технологии. Молодой ученый. — 2017. — Т. 135, № 1. — C. 4–7.
- Гукетлев Ю. Х. и др. Лазерная технология интегральных схем. — Москва.: Радио и связь, 1991. — 319 с.
- Вейко В. П., Метев С. М.. Лазерные технологии в микроэлектронике. — София: Издание БАН, 1991. — 487 с.
4. Zehner D. M., White C. W., Ownby L. Preparation of atomically clean silicon surfaces by pulsed laser irradiation. — Appl. Phys. Letters, 1980, v. 36, № 1, p. 56–59.
- Bermudez V. M. Changes in the surface composition of Si, TiO2, and SiO2 induced by pulsed ruby-laser irradiation. — J. Vacuum Sci. and Technology, 1982, v. 20, № 1, p. 51–57.
- Наумченко А. С., Светличный А. М. Руководство к лабораторным работам по курсу “Технология микросистем”. — Таганрог: Издательство технологического института при Южном Федеральном Университете, 2010. — 37 с.
- Osgood R. M., Sanchez R. A., Ehrlich D. T. e. a. Localized laser etching of compound semiconductors in aqueous solution. — Appl. Phys. Letters, 1982, v. 40, № 5, p. 391–395.
- Fowler A. B., Hodgson R. T. Selective laser annealing. — Appl. Phys. Letters, 1980, v. 36, № 11, p. 914–915.