Сущность процесса хонингования
В настоящее время в серийном и массовом производстве при изготовлении ответственных деталей предъявляются высокие требования к точности и шероховатости поверхности: некруглость менее 1 мкм, волнистость менее 0,2 мкм, нецилиндричность и непрямолинейность образующей менее 2–5 мкм, параметр шероховатости Ra = 0,02- 0,8 мкм, отсутствие дефектного слоя металла (структурно-фазовых изменений, напряжений растяжения, микротрещин), определенные значения параметров формы микронеровностей и опорной поверхности. [1]
Обеспечение этих требований достигается с помощью таких процессов абразивной обработки, как хонингование брусками из традиционных и сверхтвердых абразивных материалов. Этот процесс относят к процессу доводки; хонингование производится при одновременно выполняемых вращательном и возвратно-поступательном движениях инструмента (головки с брусками). В отличие от шлифования, при котором контактная поверхность составляет незначительную часть рабочей поверхности круга, при хонинговании брусок постоянно соприкасается с деталью по всей рабочей поверхности, причем в начальный момент времени брусок прирабатывается к обрабатываемой поверхности. Такой контакт пары брусок — заготовка способствует повышению производительности обработки и точности формы деталей. Давление при хонинговании на поверхности контакта бруска с деталью составляет 0,1–1 МПа, что в 10–100 раз меньше, чем давление при шлифовании. Скорость резания при обработке брусками 10–100 м/мин, т. е. в 15–100 раз ниже, чем при шлифовании. В результате при хонинговании тепловыделение в зоне обработки значительно ниже, чем при шлифовании, а контактная температура не превышает 150–200 ° С. [2] Таким образом, отсутствуют физические причины образования в поверхностном слое микротрещин и прижогов, а также остаточных напряжений растяжения. На рисунке 1 приведена схема рабочего движения. Подача (разжим) брусков в радиальном направлении при хонинговании производится либо непрерывно, под воздействием постоянного усилия, либо периодически, на каждый двойной ход хонинговальной головки.
Рис. 1. Схема движений бруска и детали при хонинговании: 1 — деталь; 2 — брусок; 3 — перебег; 4 — перекрытие (Vок — окружная скорость, Vвп — скорость возвратно-поступательного движения, αс — угол сетки)
При контакте рабочей поверхности бруска с обрабатываемой поверхностью заготовки происходит царапанье металла одновременно большим числом абразивных частиц. Размер таких частиц при хонинговании составляет 20–100 мкм, среднее число частиц на поверхности бруска 20–400 зерен на 1 мм2. Основными видами взаимодействия абразивных зерен с металлом являются микрорезание со снятием тончайших стружек и трение с пластическим оттеснением металла. Для интенсивного резания необходимо, чтобы абразивный брусок самозатачивался путем скалывания и вырывания затупившихся зерен из связки. При использовании брусков из сверхтвердых абразивных материалов (алмаза, эльбора) зерна длительное время сохраняют свою остроту, преобладает микроскалывание зерен, а не вырывание их, что значительно повышает стойкость брусков.
Путем выбора оптимальных характеристик брусков и регулирования параметров обработки (скорости, давления) можно управлять процессом обработки, осуществляя на первой стадии непрекращающееся резание металла в течение достаточно длительного времени, необходимого для исправления погрешностей формы заготовки, удаления исходной шероховатости и дефектного слоя. Скорость съема металла при этом составляет 2–4 мкм/с. Для получения поверхности с малой шероховатостью (Ra= 0,1–0,3 мкм при хонинговании), а также для создания благоприятного микрорельефа поверхности деталей и упрочненного поверхностного слоя металла процесс обработки на заключительной стадии может быть переведен в режим преобладающего граничного трения, при котором съем металла резко сокращается, а брусок выглаживает обрабатываемую поверхность. Такой переход можно осуществить, изменяя параметры обработки: повышая окружную скорость заготовки или инструмента, снижая давление бруска и частоту колебаний бруска. [3]
Процесс хонингования двигателя внутреннего сгорания
Обычно процесс хонингования двигателя происходит в два этапа. Первый этап — это черновая обработка цилиндров, для которой применяют крупный абразив. Второй этап — это окончательная или финишная обработка. Тут уже в дело вступает мелкозернистый абразив, который дает большую точность обработки. В качестве абразивов для хонингования цилиндров используют алмазные и керамические бруски. Последние уступили место алмазным абразивам по ряду причин: это долговечность и меньшая итоговая цена алмазного хонингования. На рисунке 2 показаны цилиндры двигателя внутреннего сгорания после операции хонингования:
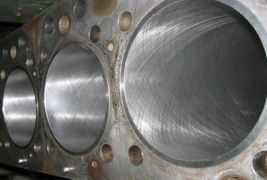
Рис. 2. Цилиндры двигателя внутреннего сгорания после операции хонингования
Достоинства хонингования
При капитальном ремонте происходит расточка цилиндров до ремонтного размера. Но чтобы сохранить правильную форму цилиндров двигателя и достичь оптимальной шероховатости применяют хонингование. Хонингование цилиндров двигателя — это финишный этап в обработке и капитальном ремонте мотора. По сравнению с традиционными доводочными операциями, такими как полирование или притирка требуемой поверхности, хонингование обладает большей точностью и большей эффективностью. Плосковершинное хонингование имеет ряд преимуществ. Его основная задача — эта тщательная обработка цилиндров двигателя для последующей работы. В результате хонингования цилиндры и поршневые кольца быстрее прирабатываются, а значит будет меньший износ деталей и повысится эффективность работы. За счет быстрой приработки деталей повышается компрессия в цилиндрах и увеличивается срок службы двигателя до следующего капитального ремонта. Также, значительно уменьшается расход моторного масла и сокращается прорыв газов в картер. Еще одна особенность хонингования двигателя — это образование на цилиндрах некой сетки, которую можно заметить лишь при тщательном осмотре. Она нужна для того, чтобы удерживать масло на стенках цилиндров мотора, в результате чего повышается обильная смазка трущихся деталей двигателя внутреннего сгорания.
Литература:
- З. И. Кремень, И. Х. Страшевский '' Хонингование и суперфиниширование деталей'' Ленинград, ''Машиностроение'' 1988г.
- Бабичев А. П. '' Хонингование'' М. ''Машиностроение'' 1965г.
- Прогрессивные методы хонингования М. ''Машиностроение'' 1981г.