Анализ нормативно-технической документации показал, что параметры ультразвукового контроля в большинстве случаев выбираются без учета фактической скорости распространения продольной и поперечной волн в материале, что приводит к неточности в определении координат расположения дефекта. В статье приведены результаты экспериментальных измерений скоростей в восьми тест-образцах, изготовленных из сталей различного назначения. На основании полученных результатов проведена оценка погрешности при определении координат дефектов с учетом изменении скорости распространения поперечной волны в материале.
Ключевые слова: ультразвуковой контроль, поперечная и продольная волна, дефект, определение координат.
Эффективность применения ультразвукового контроля, определяется не только поиском, но и правильной оценкой выявленных несплошностей. При этом оценка качества контролируемого объекта проводится не только по амплитуде отраженного импульса, но и по расположению в сечении контролируемого объекта поверхности, вызвавшей отражение [1, с.1].
В настоящее время, эксплуатирующие и ремонтные организации требуют, по возможности, точно определять истинное местоположение несплошности. Для того чтобы избежать многократных и необоснованных ремонтов, т. к. это серьезная экономическая проблема, поскольку необоснованный ремонт не только приносит убытки в сотни тысяч рублей, но и ухудшает качество сварного соединения и примыкающих к нему зон, что в будущем может стать причиной аварии.
Местоположение дефекта в сварных соединениях определяют по координатам: H — глубина залегания дефекта, X — проекция расстояния вдоль поверхности изделия от точки выхода ПЭП до дефекта (рис.1).
Рис. 1. Координаты расположения несплошности при ультразвуковом контроле
Программное обеспечение современных дефектоскопов для автоматического определения координат Х и Н дефекта позволяет устанавливать значение скорости поперечной волны, угол ввода. Глубиномерное устройство измеряет временной интервал между зондирующим импульсом и эхо-сигналом от отражателя Т, а расчет координат Х и Н производится по формулам (1) и (2):

, (2)
где r — расстояние от точки выхода до отражателя по лучу, T — время распространения от пьезоэлемента до отражателя и обратно, — время распространения ультразвуковых колебаний (УЗК) в призме преобразователя,
— скорость поперечной волны в контролируемом объекте,
— угол ввода.
Совершенные ранее открытия показали, что погрешность измерения координат определяется отклонением истинных значений скорости распространения ультразвука в материале и угла ввода от предполагаемых величин [2, с.233].
Известно, что скорость связана с упругими константами. В свою очередь, упругие константы зависят от структуры и химического состава сплавов. Для оценки влияния скорости распространения УЗК на погрешность определения координат были отобраны 8 стальных тест-образцов (рис. 2). Для определения марки стали был проведен химический анализ данных образцов.
Рис. 2. Стальные тест-образцы
Измерения скорости продольной волны выполнены c применением дефектоскопа А1212 MASTER и стационарного измерителя скорости распространения продольных и поперечных волн УЗК повышенной точности УЗИС-ГЭТУ [3, с.297], с точностью не хуже 0,5 % (табл. 1).
Таблица 1
Результаты экспериментальных измерений скорости УЗК
№тест-образца |
Марка стали |
Скорость продольной волны (УЗИС-ГЭТУ) |
Скорость продольной волны (А1212) |
Скорость поперечной волны (УЗИС-ГЭТУ) |
Скорость поперечной волны (А1212) |
1 |
15Х5М |
5,915±0,03 |
5,945±0,06 |
3,281±0,02 |
3,293±0,04 |
2 |
Ст3сп |
5,870±0,03 |
5,790±0,06 |
3,249±0,02 |
3,252±0,04 |
3 |
08Х18Н10Т |
5,688±0,03 |
5,628±0,06 |
3,126±0,02 |
3,136±0,04 |
4 |
12Х1МФ |
5,900±0,03 |
5,924±0,06 |
3,240±0,02 |
3,253±0,04 |
5 |
20 |
5,795±0,03 |
5,824±0,06 |
3,236±0,02 |
3,242±0,04 |
6 |
45 |
5,840±0,03 |
5,905±0,06 |
3,245±0,02 |
3,237±0,04 |
7 |
20Х13 |
5,940±0,03 |
5,946±0,06 |
3,309±0,02 |
3,323±0,04 |
8 |
1.4852 |
5,877±0,03 |
5,860±0,06 |
3,215±0,02 |
3,206±0,04 |
Проведенный анализ результатов экспериментальных измерений показал, что в тест-образцах № 1, № 3, № 7, № 8 изменение скорости (относительно справочного значения 3,25 мм/мкс) продольной волны составляет 0,25 … 0,7 %, скорости поперечной (0,95 … 2,3 %).
Для точной работы глубиномерного устройства дефектоскопа необходимо ввести несколько параметров: время в ПЭП (







, (3)
где ,
На основе результатов экспериментальных исследований (табл. 1) и формулы (3) построен график расчетных значений погрешности при определении глубины расположения отражателя в зависимости от угла ввода
(рис.3).
Рис. 3. Расчетные зависимости погрешности определения глубины расположения отражателя от угла ввода
(без учета параметров ПЭП)
По графику (рис.3) погрешность близка к нулю при
=
и возрастает с увеличением угла ввода
Например: при
=60
и
погрешность
= — 4 %, а при
=65
и
погрешность
= — 9 % [2, с.298]. Построенный график (рис. 3) рассчитан без учета фактического значения скорости в мере СО-3, на которой определяется «задержка» в призме. В дальнейшем это может привести к расхождению измеренных и фактических значений координат расположения дефектов.
Для учета компенсации временного интервала Т распространения УЗК в призме подставим в формулу (3) значения времени распространения, , Т1
=
,
=
,
где r — путь до вогнутой поверхности меры СО-3, — время распространения УЗ в мере СО-3 с предполагаемым значением скорости
,
— время распространения УЗ в мере СО-3 с фактическим значением скорости
.
В результате подстановки получена формула (4), позволяющая определить зависимость погрешности определения глубины расположения отражателя от угла ввода
:
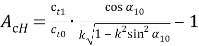
По полученной формуле (4) построен график зависимости (рис.4) суммарной погрешности при изменении скорости поперечной волны в мере СО-3 и контролируемом объекте. При этом величина погрешности увеличилась относительно предыдущего графика на 1–3 %.
Рис. 4. Расчетные зависимости погрешности определения глубины расположения отражателя от угла ввода
(с учетом параметров ПЭП)
По формуле (5) построен график (рис.5) зависимости суммарной погрешности определения координаты Х расположения отражателя от угла ввода
:
. (5)
Рис. 5. Расчетные зависимости погрешности определения координаты Х расположения отражателя от угла ввода
Погрешность не зависит от угла ввода, а зависит только от изменения скорости поперечной волны в изделии. Для определения координат обнаруженного дефекта, при углах ввода свыше 55
целесообразно определять местоположение отражателя путем измерения координаты X [2, с.236].
Приведенные в данной статье результаты экспериментальных исследований показали, что при изменениях скорости (до 3 %) погрешность в определении координат достигает 15 %, а с учетом изменения скорости в мере СО-3 погрешность дополнительно увеличивается на 1–3 %.
Поэтому еще раз подчеркивается необходимость определения скорости как в мерах или образцах для настройки основных параметров, так и в контролируемом объекте. В связи с данными обстоятельствами встает острая необходимость разработки экспресс-методики, которая позволит определять скорости распространения УЗК с высокой точностью.
Литература:
- Гурвич А. К., Г. Я. Дымкин Г. Я. Измерение координат отражателей (дефектов) при ультразвуке контроле эхо-методом. — СПб.: Типография ФГБОУ ВО ПГУПС, 2017. — 9 с.
- Алешин Н. П., Белый В. Е., Вопилкин А. Х., Вощанов А. К., Ермолов И. Н., Гурвич А. К. Методы акустического контроля металлов. — СПб.: Машиностроение, 1989. — 450 с.
- Шевелько М. М., Перегудов А. Н., Яковлев Л. А., Ковалевский М. В. Измеритель скорости ультразвука повышенной точности УЗИС-ГЭТУ // Труды Нижегородской акустической сессии. — 2002. — С. 297–299.