Одним из основных путей повышения эффективности строительства скважин является совершенствование и развитие приемов проектирования профиля и траектории наклонно направленных и горизонтальных скважин (ННС и ГС).
На настоящее время рядом научно-исследовательских работ теоретически и экспериментально обоснована и подтверждена эффективность использования роторно-управляемых систем (РУС) при строительстве сложных ННС и ГС с непрерывной кривизной траектории без зон взаимодействия на базе плоских трансцендентных кривых.
На настоящее время существует большое количество разнообразного программного обеспечения (ПО), с помощью которого проектными организациями производится выбор наиболее эффективных профилей и траектории скважины с учетом ряда параметров и закономерностей, присущих тем или иным месторождениям Западной Сибири с целью минимизации действующих нагрузок и сил трения на скважину и компоновку бурильных труб и как следствие предотвращение воздействия различных неблагоприятных явлений.
На современном этапе в виде модернизированного решения, ориентированного на минимизацию сбоев и увеличение уровня разработки скважин с существенным отклонением от вертикали наличествует тренд роста спроса на применение РУС, которые позволяют вести непосредственный контроль буровыми процессами и возможность ориентируемого бурения в режиме реального времени [5]. На настоящее время около 25 % строительства ННС и ГС производится с применением РУС.
Однако, несмотря на высокую эффективность РУС, существует рад сложностей связанных с наличием сложного геологического строения месторождений с многочисленными включениями разнообразных по составу пропластков, с различными физическим и механическими характеристикам в разбуриваемых горизонтах которые могут в процессе набора или снижения зенитного и азимутального углов с интенсивностью 0,5–2,5°на протяженных ННС и ГС могут привести к потери устойчивости буровой колонны (БК) возникновению явления неконтролируемых торсионных колебаний и как следствие к повреждению управляемых элементов РУС [8].
Одним из основных требований при выполнении буровых работ является попадание компоновки низа КНБК в заданный проектной документацией круг допуска созданием определенной модели траектории скважины с обеспечением доведения осевой нагрузки на породоразрушающий буровой инструмент, с одновременным контролем и регулировкой сил трения и действующих нагрузок препятствующих протягиванию колонны буровых труб (КБТ) по скважине, контролировать действия растягивающих, сжимающих сил и скручивающими напряжениями, которые влияют на ограничение буровых и эксплуатационных возможностей работы БК [10, 12].
Данное ограничение зависит от технологических параметров и технических характеристик принятого оборудования в составе БК, их прочностными свойствами, которые являются обоснованием для принимаемых параметров траектории и профиля скважины [1].
Анализ различных исследований создает все необходимые предпосылки для разработки комплексного алгоритма оценки с учетом ряда технических и технологических факторов, разработанных конкретно для каждого месторождения по их горно-геологической структуре, для создания наиболее эффективных и оптимальных траекторий и энергосберегающих профилей ННС и ГС, с учетом их внедрения с использованием роторно-управляемых систем [3, 11].
В результате проведения математического анализа и экспериментов были определенны основные параметры эффективности эксплуатации бурильного оборудования (рис. 1).
В процессе проведения исследования было выявлено, что кривая момента у профиля, сформированного вдоль трактрисы в скважине от 3200 метров до 2200 метров, самый маленький на данном отрезке, если сопоставлять с иными профилями (рис. 2).
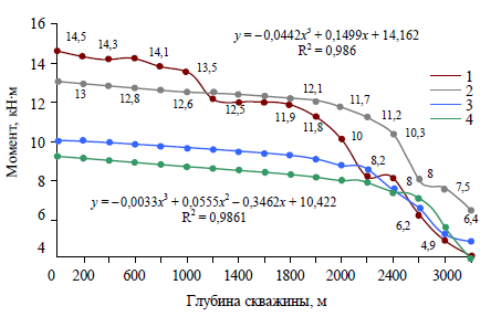
Рис. 1. Соотношение зависимости момента от дна скважины
Рис. 2. Соотношение давлений цикла и протяженности и вида профиля
Как показали результаты исследования, фактор формирования траектории ННС и горизонтального ствола на базе соотношений и взаимодействия трактрис обладает минимальной флуктуацией от идеальной модели, и, следовательно, представляется максимально удовлетворительной технологией скважинного проектирования с использованием роторно-управляемых систем.
Литература:
- Двойников M. В. Анализ проектных решений и технологических приемов проектирования и реализации профилей наклонно направленных и горизонтальных скважин // Известия вузов. Нефть и газ. 2013. № 4. С. 40–44.
- Двойников M. В. Исследование характеристик профилей наклонно направленных скважин, представленных одной линией // Бурение и нефть. 2014. № 6. С. 19–20.
- Двойников М. В. Исследования технико-технологических параметров бурения наклонных скважин // Записки Горного Института. 2017. Т. 223. С. 86–92. DOI:10.18454/PMI.2017.1.86
- Кучумов Р. Я. Программно-информационное обеспечение экспертной оценки качества гидродинамических моделей разработки месторождения методом Саати // Автоматизация, телемеханизация и связь в нефтяной промышленности. 2012.№ 6. С. 13–19.
- Разработка универсального матобеспечения для моделирования динамики колонны труб / В. С. Тихонов, А. И. Сафронов, Х. Р. Валиуллин и др. // SPE-171280-RU. 2014.
- Свидетельство о государственной регистрации программы для ЭВМ 2014617085 РФ. Метод анализа профилей скважин / А. В. Ошибков, М. В. Двойников, Ж. М. Колев, Д. Д. Водорезов. Опубл. 20.08.2014
- Farah Omar F. Direction well desing, trajectory and survey calculations, with a case study in fiale, asal rift, Djibouti /United Nations University. 2013. Orkustofnun, Grensasvegur 9. Number 27. IS-108 Reykjavik, Iceland. P. 627–623.
- Liu X. H. Downhole Propulsion/Steering Mechanism for Wellbore Trajectory Control in Directional Drilling / X. H. Liu,Y. H. Liu, D.Feng // Applied Mechanics and Materials. 2013. Vol. 318. P. 185–190.
- Saaty T. L. The Analytic Hierarchy Process. New York: McGraw Hill. 1980. 280 p.
- Samuel R. Ultra-Extended-Reach Drilling (u-ERD: Tunnel in the Earth) — A New Well-Path Design // SPE/IADC119459. 2009.
- Samuel R. Wellbore Trajectory Control Using Minimum Well Profile Energy Criterion for Drilling Automation // SPE-170861-MC. 2009.
- Zheng S. J. Calculation Method for WOB Conducting of Directional Well / S. J. Zheng, Z. Q. Huang, Wu H. J. A. // AppliedMechanics and Materials. 2013. Vol. 318. P. 196–199.