Рассмотрим основные причины выходы из строя элементов рулевого управления грузовых автомобилей малого класса. Из опыта работы предприятий автосервиса определен средний ресурс элементов, выявлен критический элемент, лимитирующий ресурс системы в целом.
Грузовые автомобили малого класса приобрели большую популярность в России. Эти автомобили хорошо подходят для перевозок небольших партий грузов, осуществляемых частными лицами, индивидуальными предпринимателями, предприятиями малой и средней мощности. В последние годы автомобили данного класса называют также коммерческими автомобилями, подчеркивая тем самым их основное назначение.
Яркими представителями автомобилей данного класса является семейство ГАЗель, Ford Transit, Volkswagen Crafter.
Автомобили рассматриваемого класса зачастую эксплуатируются в довольно жестких условиях, но при этом они демонстрируют неплохие показатели надёжности, в том числе общую долговечность. Вместе с тем, опыт работы одного из предприятий автосервиса в Волгоградской области показывает, что некоторые модели этих автомобилей обладают относительно низким ресурсом рулевого управления. Например, для одной из моделей средний ресурс рулевого управления составил 150 тыс. км, в то время как ресурс двигателя — 400 тыс. км.
Следовательно, актуальной задачей является исследование долговечности рулевого управления данной марки автомобилей, выявление критических элементов, лимитирующих ресурс, а в дальнейшем — выработка предложений по повышению долговечности этих элементов.
В рамках исследования были рассмотрены условия работы каждого элемента, входящего в систему рулевого управления, на основе чего сделаны предположения об основных причинах достижения предельного состояния. Полученные теоретические предположения были сопоставлены с данными предприятий автосервиса. Общее количество автомобилей, по которым было проведено исследование, составило 50. Преимущественно они эксплуатируются в условиях периферийных дорог, качество покрытия которых не всегда высокое. Немалая часть пробега приходится и на грунтовые дороги, в том числе глинистые и песчаные. Климат Волгоградской области — умеренный, резко континентальный, с холодной, малоснежной зимой и жарким, сухим летом. Маршрутные передвижения исследуемых автомобилей — по населенным пунктам небольшой величины и между ними. Владельцы автомобилей стремятся повысить эффективность использования подвижного состава, поэтому преимущественно автомобили движутся со значительной загрузкой.
В ходе исследования было установлено, что рулевая колонка имеет ресурс, сопоставимый с ресурсом автомобиля. Рулевой вал, труба колонки изготавливаются с высоким запасом прочности. Данные элементы долговечны. В практике эксплуатации их отказы выявлены не были.
Подшипники рулевой колонки изнашиваются медленно, однако их втулки со временем рассыпаются, в результате чего появляется люфт.
Средний ресурс втулки подшипника составляет, по данным исследования 180000 км. Внешний вид изношенных втулок представлен на рис. 1.
Рис. 1. Изношенные втулки подшипника рулевой колонки
Из анализа условий работы следует, что ресурс рулевого вала лимитируется техническим состоянием верхнего и нижнего шарниров. Исследование показало, что верхний шарнир рулевого вала имеет высокий ресурс, в то время как средний ресурс нижних шарниров составляет 130000 км.
Игольчатые подшипники крестовины со временем изнашиваются. Иглы перекатываются непосредственно по шипам крестовины, а стаканчики подшипников запрессованы в отверстия в вилках и зафиксированы от осевого перемещения. Если внутрь механизма попадает влага, смазка вымывается, а на иголках возникает коррозия, которая неизбежно приводит к полному выходу узла из строя. Крестовина либо закисает, либо разбивается и изнашивается (рис. 2).
Рис. 2. Игольчатые подшипники крестовины, подвергшиеся коррозии и разрушению
Рулевой механизм является долговечным узлом. Практика показывает, что корпус механизма, винт с шариковой гайкой и сошка практически не изнашиваются и их ресурс соответствует ресурсу автомобиля в целом.
Средний ресурс вала-сектора исследуемых автомобилей составил 350000 км. В процессе эксплуатации шлицевые поверхности вала-сектора могут иметь износ, смятие и выкрашивание. В местах работы уплотнительных колец может появиться выработка (рис. 3).
Рис. 3. Вал-сектор со следами износа
Критическими элементами рулевого механизма могут являться подшипники.
Средний ресурс подшипника винта составил 350000 км. На сепараторе опорного подшипника винта могут образоваться разломы карманов. На подшипнике образовываются трещины (рис. 4), изнашиваются дорожки качения и шарики.
Рис. 4. Трещины перегородок сепаратора подшипника
Для подшипника вала-сектора (рис. 5.) и подшипника винта был отмечен значительный разброс величины ресурса, от 110000 до 350000 км. Большая величина ресурса была достигнута в том случае, когда владелец автомобиля своевременно обращался на СТО для замены сальников.
Рис. 5. Подшипники вала-сектора
Со временем уплотнительные кольца теряют первоначальную форму, а также могут появиться надрывы и срезы (рис. 6). Средний ресурс уплотнительных колец 110000 км.
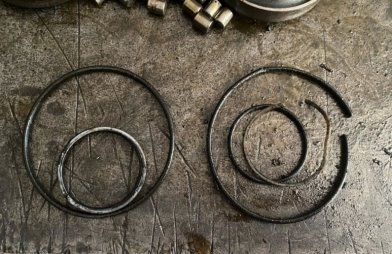
Рис. 6. Уплотнительные кольца рулевого механизма
Средний ресурс рулевых тяг 60000 км (рис. 7). Наконечник рулевой тяги защищен резиновым чехлом, с течением времени часто нарушается целостность пыльника, в шаровый шарнир попадает вода и грязь, металлические элементы корродируют, грязь действует как абразив, а вода постепенно вымывает смазку.
Рис. 7. Изношенные рулевые наконечники
Из-за воздействия нагрузок шарнирное соединение изнашивается следующим образом:
– со временем стенки вкладыша истираются, между ними и шаром образуется зазор, отчего при движении по мелким неровностям слышен негромкий стук;
– износ втулки приводит к разбалтыванию пальца, так как он прижимается пружиной только снизу.
– когда пружина и пята не в состоянии выбрать люфт, возникший в результате износа пластика, шаровый палец легко ходит во втулке.
Поворотный кулак может иметь следующие дефекты: износ посадочных поверхностей под подшипники, срыв резьбы под гайку цапфы, износ отверстий под посадку шкворней, трещины или обломы проушин. Как показывает практика, срок службы поворотного кулака значительно превышает ресурс всех остальных деталей подвески, и замена его по причине износа требуется только у автомобилей со значительным пробегом (сотни тысяч километров).
Шкворень поворотного кулака изнашивается в местах работы со втулками (рис. 8). Средний ресурс шкворня исследуемых автомобилей составляет 95000 км.
Рис. 8. Шкворень со следами износа
Виды износа втулки поворотного кулака: задиры на поверхности, коррозионный износ. Средний ресурс втулки 95000 км.
Втулка изнашивается в местах работы со шкворнями. Для более наглядного представления ее износа, втулки были развернуты (рис. 9). Можно заметить, что канавок для смазки практически нет.
Рис. 9. Изношенные втулки
В результате проведенного исследования было установлено, что элементом, лимитирующим ресурс рулевого управления в целом, является втулка шкворня поворотного кулака. У исследуемой модели автомобиля средний ресурс этой втулки составил 95 тыс. км. При этом конструкция данного узла других моделей коммерческих автомобилей практически идентична.
Следующим этапом исследования должна стать разработка мероприятий по повышению ресурса узла. Эти мероприятия включают как эксплуатационные, т. е. изменение режимов ТО, так и конструктивные.
Одним из вариантов является замена втулки шкворня на игольчатый подшипник, например, типа 943/25К. такая замена будет способствовать снижению износа в узле. Более детально влияние такой модернизации на надежность рулевого управления будет определено в ходе дальнейшего исследования.
Литература:
1. Чернышов, К. В. Показатели надёжности технических систем: наработка до отказа, ресурс, срок службы: учебное пособие. — ВолгГТУ, 2007. — 80 с.
2. Автомобили ГАЗ-3302, Руководство по эксплуатации, техническому обслуживанию и ремонту. — Москва, 2010. — 342 с.
3. Руководство по эксплуатации и ремонту Ford Transit с 2006 года выпуска с бензиновыми и дизельными двигателями. — Третий Рим, 2006. — 304 с.
4. Руководство по эксплуатации и ремонту автомобилей Mercedes-Benz Sprinter серии W906 и Volkswagen Crafter с 2006 года выпуска с бензиновыми и дизельными двигателями. — Монолит, 2006. — 446 с.