Неравномерный температурный нагрев, возникающий при сварке в элементах конструкции сопровождается появлением в них внутренних напряжений и остаточных деформаций. Прогнозирование и расчёт этих параметров является одной из приоритетных задач, так как это позволит понимать текущее состояние сварного шва, даже после длительного периода времени. В данной работе будет рассмотрена модель, достоверно отображающая распространение температурных полей, напряжений и деформаций в теле свариваемых элементов. Данная задача будет решена с помощью программного комплекса ANSYS.
Ключевые слова: сварные швы, деформации, напряжения, ANSYS, моделирование, сварка.
Процесс сварки сопровождается резким неравномерным нагревом свариваемых элементов. Область металла, попадающая в сварной шов, нагревается, а затем остывает по мере течения времени и распространения тепла в металле. В результате нагрева происходит изменение физических и механических свойств металла, что в свою очередь приводит к увеличению объёма тела во время нагрева. При последующем остывании сварного шва объём элемента уменьшается, что сопровождается линейной усадкой, однако жесткая связь шва с основным телом объекта сопротивляется этому. В результате чего появляются внутренние напряжения, а также продольные и поперечные деформации в свариваемых элементах.
Степень деформации элементов зависит от температуры нагрева и от коэффициента линейного расширения металла. Чем выше коэффициент — тем значительнее деформации.
Сложность моделирования сварных швов заключается в том, что одновременно нужно учитывать большое количество параметров, влияющих на конечный результат и достоверность исследования. В данном случае будет использоваться программный комплекс ANSYS и дополнительный модуль Moving Heat Source. В связке данный программный комплекс позволяет достаточно точно моделировать процесс сварки на всех этапах, включая фазу остывания металла с последующим анализом, появившихся в теле свариваемых объектов, остаточных деформаций.
Данная задача будет решаться в несколько этапов. Первым этапом будет создание модели исследуемого объекта. В качестве моделируемого тела была выбрана двутавровая балка, усиленная пластиной в сжатой зоне металла. Длина балки составляет 1 метр. Сварной шов будет проходить по границе стыка двутавровой балки и накладки по всей длине.
Геометрия, а также характеристики материала исследуемых элементов задаются в блоке программного комплекса — «Geometry».
На следующем этапе решения задачи моделируется воздействие окружающей среды на исследуемый объект. Задаётся постоянная температура в модуле «Transient Thermal», равная 22℃
Заключительным этапом является моделирование подвижного источника тепла, который распределяется по нормальному закону, с максимальным значением в центре. Данный подвижный источник тепла будет имитировать тепловой поток при сварке. Для решения этого этапа задача будет экспортирована в модуль «Transient Structural», где будут проанализированы напряжения, возникшие в элементе в результате неравномерного нагрева и последующего остывания, а также выявлено наличие остаточных деформаций.
В качестве материала для дискретной модели была выбрана углеродистая сталь с модулем упругости 2*10 5 МПа.
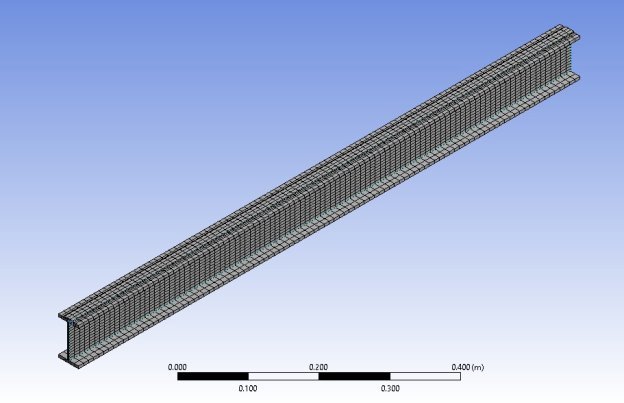
Рис. 2. Заданные характеристика материала балки
Граничные условия были приняты как две жесткие заделки с обоих концов балки, приложенные к торцевым граням модели снизу. Исследуемому объекту была задана температура окружающей среды с помощью модуля Convection, равная 22℃.
Рис. 3. Выбранный параметр окружающей среды
Рис. 4. Параметры модуля Convection
Рис. 5. График зависимости температуры от коэффициента конвекции
Далее задача экспортируется в модуль Transient Thermal для задания подвижного теплового потока. Максимальное значение находится в центре сварочной ванны, форма потока имеет конусоидальную форму. Тепловой поток воссоздан с помощью дополнительного расширения для ANSYS — Moving Heat Source. Его характеристики задаются в контекстном меню модуля. Для данного исследования скорость наложения сварного шва была принята 18 м/ч или же 5 мм/сек, а радиус луча был выбран равным 5 мм.
Рис. 6. Характеристики теплового потока
После завершения расчета задачи мы можем увидеть температурные поля, возникающие после прохождения теплового потока по поверхности металла.
Рис. 7. Распространение температурных полей в теле элемента
Анализ полученных данных показывает, что распределение температуры в теле элемента имеет «кометообразную» форму и распространяется вдоль теплового потока.
Программный комплекс также позволяет произвести анализ возникших в теле свариваемых элементов остаточных деформаций и перемещений.
Рис. 8. Максимальные перемещения
Рис. 9. Максимальные остаточные деформации
Максимальные перемещения составили 10,3 мм, а остаточные деформации — 11,2 мм.
В ходе проделанного исследования можно сделать следующие выводы:
- Полученная компьютерная модель позволяет проанализировать уже существующее или спрогнозировать дальнейшее воздействие сварных швов на элемент.
- Появляется возможность оценивать возникшие напряжения и деформации в элементе, а значит возможно создание комплекса решений прогнозирующего опасные остаточные факторы после сварки и их минимизацию.
- Возможно определение наиболее оптимального решения для нестандартной задачи, которую было бы тяжело рассчитать «вручную».
Литература:
1. Нургужин М. Р., Даненова Г. Т., Рейтаров О. В., Нурпиисова Г. Д. Компьютерное моделирование влияния механического воздействия на остаточные сварочные напряжения и деформации // Международный журнал экспериментального образования. — 2014. — № 3–1. — С.114–118.
2. Государственный проектный и научно-исследовательский институт (Укркинпроектстальконструкция) Госстроя СССР Пособие по проектированию усиления стальных конструкций (к СНиП II-23–81*).
3. Денисов М. А. Компьютерное проектирование. Ansys // Учебное пособие. Екатеринбург, Издательство Уральского университета 2014.