В данной статье представлена разработка и изготовление планетарного и циклоидального редуктора для испытательного стенда мобильной робототехнической системы. Механические компоненты были задуманы с возможностью использования аддитивного производства и готового оборудования, чтобы ограничить затраты и время, затрачиваемые на создание прототипов.
Ключевые слова: электромеханический привод; аддитивное производство; планетарный редуктор; циклоидальный редуктор.
Для изготовления деталей редукторов необходимо выполнить инженерный расчет. Проектировались два редуктора: планетарный и циклоидальный редукторы.
Проектирование планетарного редуктора
Перед проектированием необходимо выполнить некоторые расчеты, чтобы определить передаточное число или количество зубьев, необходимых для каждой части системы редуктора.
Чтобы зубчатая передача работала должным образом (1), важно, чтобы количество зубьев коронной шестерни равнялось количеству зубцов солнечной шестерни плюс удвоенное количество зубцов планетарной шестерни [1,2].
R = 2 × P + S (1)
Формула (2), которая помогает определить передаточное число для системы:
(R + S) ×Ty = Ts × S (2)
Где:
R — количество зубьев коронной шестерни;
S — количество зубьев солнечной шестерни;
P — количество зубьев сателлитов;
Ty — скорость вращения водила;
Ts — скорость вращения солнечной шестерни.
i — передаточное соотношение.
Следующее уравнение позволяет рассчитать скорость вращения солнечной шестерни или водила.
Ty = Ts × [S/(R + S)] (3)
Ts = [(R + S)/S] ×Ty (4)
На основании приведённых формул были полученные результаты, показанные в таблице 1.
Таблица 1
Данные полученные при расчетах
R |
S |
P |
Ty |
Ts |
i |
35 |
11 |
12 |
300 |
1200 |
4 к 1 |
Рис. 1. Спроектированный планетарный редуктор
При помощи полученных результатов спроектирован планетарный редуктор для робототехнических систем показанный на рисунке 1. При помощи аддитивных технологий, а именно на 3D-принтере напечатаны шестерни и корпус редуктора, что показано на рисунке 2.
Рис. 2. Нога робота, изготовленная на 3D-принтере
Проектирование циклоидального редуктора
Входной вал приводит в действие эксцентриковый подшипник, который, в свою очередь, приводит в движение циклоидальный диск эксцентричным циклоидальным движением. Периметр этого диска соединен с неподвижной коронной шестерней и имеет ряд штифтов или роликов выходного вала, расположенных через поверхность диска. Эти пальцы выходного вала непосредственно приводят в движение выходной вал при вращении циклоидального диска. Радиальное движение диска не передается на выходной вал [3]. Перед проектированием необходимо провести расчеты, чтобы определить: количество штифтов коронной шестерни (N), количество выступов на циклоидальном диске (n), эксцентриситет (е), диаметр циклоидального диска (d), диаметр штифтов (
В таблице 2 представлены полученные при расчетах значения для дальнейшего проектирования редуктора.
Таблица 2
Данные полученные при расчетах
D |
d |
e |
N |
n |
|
45 мм |
42,55 мм |
1,225 мм |
20 |
19 |
3,516 мм |
На рисунке 3 представлен спроектированный циклоидальный редуктор по полученным при расчете данным. Редуктор также был напечатан на 3D-принтере
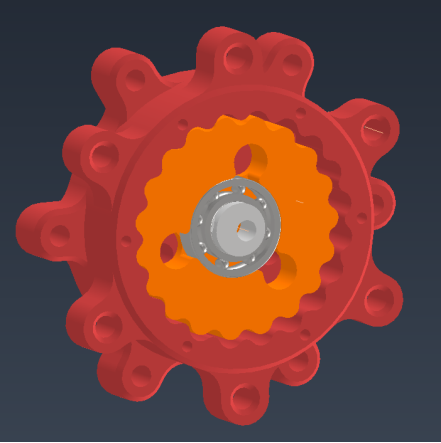
Рис. 3. 3D-модель циклоидального редуктора
Преимущества и ограничения аддитивного производства на 3 D -принтере
При проектировании испытательного стенда широко использовалась 3D печать для сокращения затрат и времени на создание прототипов редукторов. По той же причине, где это было возможно, использовались легкодоступные готовые компоненты.
Использование 3D-печати, как и любой другой производственной технологии, необходимо учитывать, начиная с ранних этапов проектирования механического оборудования. Этот метод предлагает несколько преимуществ по сравнению с традиционными технологиями. Во-первых, можно работать с очень сложной геометрией без дополнительных процессов, необходимых для производства. По этой причине можно с самого начала проектировать детали со структурным облегчением, ребрами жесткости и шарнирной трехмерной геометрией, не уделяя чрезмерного внимания ограничению требуемых процессов. Кроме того, количество деталей в сборке может быть значительно уменьшено, поскольку сложные компоненты могут быть изготовлены как одно целое.
Аддитивное производство позволило снизить затраты на изготовление прототипа планетарного редуктора; некоторые детали было бы сложно производить с использованием традиционных технологий, а стоимость одного прототипа была бы очень высокой без преимущества масштабного производства.
При 3D печати можно столкнуться с некоторыми ограничениями при использовании для производства функциональных механических компонентов. Во-первых, механические свойства большинства материалов для печати плохие; прочность на разрыв пластика ABS и PLA составляет порядка 30 МПа с модулем упругости от 1,2 до 3,5 ГПа. Эти свойства относятся к основному материалу и зависят от процесса печати [4, 5]. Твердость поверхности также низкая, и следует избегать высокого контактного давления при соединении компонентов.
Кроме того, некоторые смазочные материалы, обычно используемые для металлических деталей, химически несовместимы с пригодными для печати полимерами. Имеется мало литературы относительно совместимости смазочных материалов с полимерами для печати. Однако, похоже, что большинство минеральных и синтетических масел и смазок имеют тенденцию разрушать PLA и ABS [6]. Погружение образца PLA в силиконовую смазку на неделю не привело к значительному изменению его механических свойств. Поэтому мы решили использовать его в качестве смазки для коробки передач.
Вывод
Планетарный и циклоидальный редукторы были разработаны и изготовлены для мобильной робототехнической системы. Отсутствие гибких компонентов приводит к более высокой жесткости и большей устойчивости к усталостным повреждениям. Дополнительными преимуществами предлагаемой конфигурации являются низкая инерция. В результате достигается хорошая устойчивость к высокому крутящему моменту и высоким радиальным нагрузкам.
Большинство компонентов сборки было произведено с использованием 3D печати, чтобы снизить затраты и быстро изготовить функциональный прототип. В результате мы получили несколько уроков, извлеченных для создания прототипов функциональных механических деталей с помощью недорогих методов аддитивного производства, в частности 3D-печати. Были рассмотрены ограничения материалов с точки зрения плохих механических свойств и химической совместимости со смазочными материалами, а геометрия компонентов была определена с учетом возможностей выбранной технологии производства.
Дальнейшая работа будет включать количественную оценку трения и механической эффективности, как в условиях вспомогательной, так и противодействующей нагрузки, а также сравнение с экспериментальными результатами.
Литература:
- Ликин, А. М. Механический привод с цилиндрическим редуктором: учебно-методическое пособие к курсовому проекту по дисциплине «Детали машины и основы конструирования» / А. М. Ликин, В. Н. Никитин. — Омск: СибАДИ, 2014. — 68 c.
- Чернавский, С. А. Проектирование механических передач: учебно-справочное пособие для вузов / С. А. Чернавский, Г. А. Снесарев, Б. С. Козинцов. — Москва: Альянс, 2008. — 590 c.
- He, W.D.; Li, L.X.; Li, X. New optimized tooth-profile of cycloidal gear of high precision RV reducer used in robot. Chin. J. Mech. Eng. 2000, 36, 51–55.
- Brischetto, S.; Torre, R.; Ferro, C. G. Experimental evaluation of mechanical properties and machine process in fused deposition modelling printed polymeric elements. Adv. Intell. Syst. Comput. 2020, 975, 377–389.
- Brischetto, S.; Ferro, C.G.; Torre, R.; Maggiore, P. 3D FDM production and mechanical behavior of polymeric sandwich specimens embedding classical and honeycomb cores. Curved Layer. Struct. 2018, 5, 80–94.
- Cavestri, R. C. Compatibility of refrigerants and lubricants with engineering plastics. In Final Report Prepared for the Air-Conditioning and Refrigeration Technology Institute Under ARTI MCLR Project Number 650–50600; Imagination Resources, Inc.: Dublin, OH, USA, 1 December 1993.