В статье оценивается стойкость стеклянных волокон в среде гидратирующего портландцемента. Оценка стойкости производится по результатам контроля прочности на растяжение при изгибе и при сжатии стандартных образцов-балок, изготовленных из цементного теста нормальной густоты. Испытаниям подвергались серии неармированных образцов и образцов, армированных стеклянной фиброй. Образцы этих серий испытывались в разном возрасте, при этом, одна часть образцов твердела и набирала прочность в воде, а другая часть образцов подвергалась тепловлажностной обработке в лабораторной пропарочной камере.
Ключевые слова: фиброцемент, прочность на растяжение при изгибе, прочность при сжатии, стеклянная фибра, цементный камень.
В настоящее время на кафедре технологии строительных материалов и метрологии Санкт-Петербургского государственного архитектурно-строительного университета продолжается исследование свойств фибробетонов, изготовленных с применением различных видов волокон, а также изготовленных на основе различных матриц.
Фибробетоном называют композиционный материал, который представляет собой бетонную матрицу, по всему объему которой равномерно распределены дискретные волокна.
Волокна можно классифицировать в зависимости от их модуля упругости. Волокна, модуль упругости которых меньше модуля упругости тяжелого бетона, относят к категории низкомодульных волокон, а волокна с более высоким, по сравнению с тяжелым бетоном, модулем упругости — к категории высокомодульных [1, 2, 3].
Совершенно очевидно, что введение тех или иных волокон в состав бетона будет влиять на свойства получаемых композитов, в том числе, на прочность на растяжение при изгибе и на прочность при сжатии.
При определении состава фибробетона имеет большое значение выбор матрицы, в частности, выбор вяжущего для ее изготовления. При изготовлении матрицы могут быть использованы воздушные и гидравлические вяжущие, например, гипсовое вяжущее или портландцемент и его разновидности. Следует отметить, что среда гидратирующего гипсового вяжущего является кислой, а гидратирующего портландцемента — щелочной. Некоторые разновидности армирующих волокон могут быть не стойкими к указанным средам. Например стальные волокна будут корродировать в кислой среде, тогда как щелочная среда может оказаться агрессивной к некоторым волокнам минерального происхождения.
В данной статье рассматривается вопрос стойкости стеклянных волокон в щелочной среде гидратирующего портландцемента.
Стеклянные волокна обладают высокой прочностью — до 2500МПа и высоким модулем упругости — 73000МПа, в связи с чем, представляется перспективным введение таких волокон в состав фибробетона для повышения его прочности. При этом стеклянные волокна имеют существенный недостаток — низкая коррозионная стойкость к щелочам.
Гидратация минералов портландцементного клинкера происходит с образованием, в том числе, гидроксида кальция, активно взаимодействующего с компонентами стекла. В результате воздействия щелочесодержащей жидкой фазы твердеющего цемента происходит коррозионное разрушение стеклянных волокон вследствие выщелачивания и разрушения их кремнекислородного каркаса при контакте с этой средой.
Одним их наиболее распространенных стекол, используемых при изготовлении стекловолокна, в настоящее время, является алюмоборосиликатное стекло. По некоторым данным такое стекло достаточно активно взаимодействует с гидроксидом кальция гидратирующего портландцемента, но превосходит по щелочестойкости обыкновенное кварцевое стекло [4].
В данной статье рассматривается волокно из стекла алюмоборосиликатного состава по причине его широкой распространенности.
Для оценки щелочестойкости стекла можно применить ГОСТ 10134.3–2017 «Стекло и изделия из него. Методы определения химической стойкости. Определение щелочестойкости». В соответствии с методикой указанного ГОСТа, следует кипятить образец стекла в растворе карбоната натрия и гидроксида натрия в течении трех часов. Щелочестойкость стекла определяется отношением потери массы после кипячения к площади поверхности стеклянного образца.
В одном из найденных источников описывается более сложный эксперимент [4]. Устойчивость опытных составов стекол и стекловолокон к воздействию насыщенного раствора гидроксида кальция исследовали методом определения активности гидравлических добавок и оценивали по количеству Ca(OH) 2 в пересчете на CaO, поглощенного 1 г стеклопорошка.
Эксперимент, описываемый в данной статье, состоит в том, чтобы оценить снижение прочности фиброцемента во времени. Для проведения данного эксперимента были изготовлены 4 серии образцов-балочек размерами 4×4×16 см, всего 96 образцов. Образцы испытывались на прочность на растяжение при изгибе, а полученные при этом половинки — на прочность при сжатии. Первая серия образцов цементного камня изготовлена из цементного теста нормальной густоты, а другая серия — также изготовлена из цементного теста нормальной густоты, но в его состав введена стеклянная фибра в количестве 1 % об. 2 серии образцов, на вторые сутки после формования, распалубливались и погружались в воду, где происходило их дальнейшее твердение и набор прочности. При этом, с интервалами в 2–5 суток производились испытания образцов. Параллельно, испытывались аналогичные серии образцов, но они хранились не в воде, а проходили тепловлажностную обработку в лабораторной пропарочной камере по режиму 2+4+2 (подъем температуры до 80°С, ч, экзотермическая выдержка при 80°С, ч, охлаждение, ч). Пропаренные образцы подвергались испытаниям, также с интервалами 2–5 суток, одновременно с испытаниями образцов из первых двух серий. Такой режим испытаний обусловлен возможностью использования лабораторной пропарочной камеры.
При проведении исследования был использован портландцемент ЦЕМ I 42,5 Н Сланцевского цементного завода и стекловолокно длиной 18мм, диаметром 10–16 мкм, производства Qingdao Junfeng Industry Company Limited, алюмоборосиликатное (по маркировке производителя E-glass), представленное на рис.1.
Рис. 1. Стеклянная фибра
Все образцы первых двух серий находились в воде все время, от момента распалубки, до момента проведения испытаний, а другие две серии- в пропарочной камере. Периодически проводилась ТВО. Испытания образцов проводились после каждого цикла ТВО, для этого, из всех образцов находящихся в пропарочной камере, отбиралось несколько штук для испытаний, а остальные оставались в камере для прохождения последующих циклов ТВО. Тоже самое происходило и с образцами, твердевшими в воде. Таким образом, а по мере проведения эксперимента, пропариваемые образцы, набирали все большее количество циклов ТВО, а образцы, твердеющие в воде — все больший возраст. Вначале определялась прочность на растяжение при изгибе и при сжатии пропаренных образцов цементного камня и стеклофиброцемента, а затем проводились такие же испытания образцов, твердевших в воде. Последние образцы из первых двух серий набирали прочность в воде в течении 32 суток, а пропариваемые прошли 8 циклов ТВО.
Результаты испытаний образцов цементного камня представлены на рис. 2.
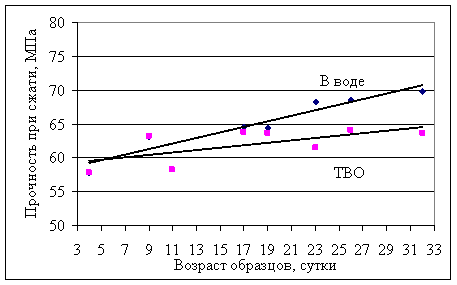
Рис. 2. Результаты испытаний цементного камня на прочность при сжатии
На рис. 3 представлены результаты испытаний прочности на растяжение при изгибе тех же образцов.
Рис. 3. Результаты испытаний цементного камня на прочность на растяжение при изгибе
По представленным на рис. 2 и 3 данным видно, что образцы, твердевшие в воде, имеют более высокие значения прочности, чем пропаренные. Это объясняется тем, что тепловлажностная обработка в пропарочной камере, не позволяет, при прочих равных условиях, получить равную прочность с образцами, набиравшими ее в воде. Прочность пропаренных образцов снижена из-за неравного термического расширения воды, цемента, продуктов его гидратации, а также образующегося цементного камня [5].
Так же следует отметить, что прочность образцов цементного камня на растяжение при изгибе практически не изменяется с течением времени, это показывает, что цементный камень набирает ее менее чем за 4 суток.
На рис. 4 представлены результаты испытаний прочности стеклофиброцементных образцов при сжатии.
Рис. 4. Результаты испытаний стеклофиброцемента на прочность при сжатии
На рис. 5 представлены результаты испытаний прочности стеклофиброцементных образцов на растяжение при изгибе.
Рис. 5. Результаты испытаний стеклофиброцемента на прочность на растяжении при изгибе
По представленным на рис. 4 данным видно, что прочность при сжатии стеклофиброцемента повышается с течением времени. Образцы, набиравшие прочность в воде, на 4 сутки имеют прочность 51МПа, а на 32 сутки — 67МПа (по аппроксимирующей зависимости), при этом, образцы из цементного камня имеют, в то же время, соответственно 56 МПа и 71 МПа, то есть тенденция к повышению прочности в обоих случая составляет примерно 15–16 МПа. Прочность стеклофиброцемента оказалась, во всем диапазоне, на 4 -5 МПа ниже (8–10 %), это можно объяснить влиянием стеклянной фибры на консистенцию фиброцементной смеси. Стекловолокно вводилось в цементное тесто нормальной густоты в количестве 1 % об., что привело к снижению подвижности, и, как следствие, недостаточному уплотнению смеси при изготовлении образцов. Аналогичную тенденцию можно заметить и на образцах прошедших ТВО. Получается, что существенного влияния армирование цементного камня стекловолокном на его прочность при сжатии не оказывает.
Как было отмечено выше, цементный камень набрал максимальную прочность на растяжение при изгибе менее чем за 4 суток, при этом она составила примерно 11 МПа, при твердении в воде и 7 МПа после 8 циклов ТВО.
Образцы из фибростеклоцемента на 4 сутки твердения в воде показали примерно 14,1 МПа, а на 32 сутки — 13,3МПа (по аппроксимирующей зависимости). Снижение прочности на 5,7 % не следует считать показательным, поскольку коэффициент вариации данных значений составил 12,6 %. Получается, что введение в цементный камень 1 % об. стекловолокна привело к повышению его прочности на растяжение при изгибе на 24,7 %.
Прочность фибростеклоцемента на растяжение при изгибе после первого цикла пропаривания составила 6,5 МПа, а после восьмого — 6,3 МПа (по аппроксимирующей зависимости), то есть практически не изменилась. Прочность фибростеклоцемента на растяжение при изгибе оказалась меньше прочности цементного камня на 7,1 %, что так же можно объяснить недоуплотнением смеси при изготовлении образцов.
Получается, что при твердении образцов в воде прочность фиброцемента оказалась выше на 24,7 %, а при пропаривании не изменилась. Это можно объяснить тем, что стекловолокно из алюмоборосиликатного стекла за 32 дня корродирует в среде гидратирующего портландцемента не существенно. На рис.6 представлена фотография поверхности разлома одного из испытанных образцов, твердевшего в воде в течении 32 суток.
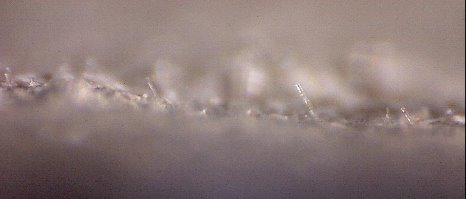
Рис. 6. Поверхность разлома стеклофиброцементного образца после твердения в воде
На фотографии, представленной на рис. 6, видно, что разлом пересекают стеклянные волокна, что свидетельствует об их сохранности.
На рис.7 представлена фотография поверхности разлома образца стеклофиброцемента после ТВО.
Рис. 7. Поверхность разлома стеклофиброцементного образца после 8 циклов ТВО
Обнаружить стеклянные волокна в разломах стеклофиброцементных образцов, испытанных после тепловлажностной обработки, оказалось затруднительным. На фотографии, представленной на рис. 7, видны не стеклянные волокна, а следы, образованные этими волокнами при формовании образцов, цементный камень, вблизи этих следов осветлен, очевидно, продуктами коррозии. Вероятно, это и объясняет низкую прочность пропаренного стеклофиброцемента. Одного цикла тепловлажностной обработки оказалось достаточно для такой глубокой коррозии стекловолокна, что его применение не привело к повышению прочности как в случае твердения в воде.
По результатам данного эксперимента было установлено:
- Стеклянная фибра из стекла алюмоборосиликатного состава способно выдерживать щелочную среду гидратирующего портландцемента в течении 32 суток, при условии хранения образцов в воде.
- При введении стеклянной фибры в цементное тесто удалось повысить прочность на растяжение при изгибе полученного стеклофиброцемента на 24,7 %.
- Стеклянная фибра не оказывает существенного влияния на прочность при сжатии.
- При проведении тепловлажностной обработки стеклофиброцемента, стеклянная фибра практически полностью корродирует и перестает вносить вклад в формирование его прочности.
В дальнейшем, планируется продолжить данное исследование. Предполагается провести испытания в более раннем, чем 4 сутки, возрасте, а так же продлить испытания до достижения образцами большего возраста. Кроме того, планируется провести аналогичные исследования с другими видами волокон минерального происхождения.
Литература:
- Пухаренко Ю. В. Принципы формирования структуры и прогнозирование прочности фибробетонов // Строительные материалы. 2004. № 10 (598). С. 47–50.
- Пухаренко Ю. В., Голубев В. Ю. О вязкости разрушения фибробетона // Вестник гражданских инженеров. 2008. № 3. C. 80–83.
- Пухаренко Ю. В., Голубев В. Ю. Высокопрочный сталефибробетон // Промышленное и гражданское строительство. 2007. № 9. С. 40–41.
- Рабинович, Ф. Н. Композиты на основе дисперсно-армированных бетонов. Вопросы теории и проектирования, технология, конструкции.– М.: Издательство АСВ, 2004. — 560 с.
- Баженов Ю. М. Технология бетона. — М.: Высш. шк., 1978. -455 с.