Работа посвящена распространению длинных трещин (т. е. 2–3 мм и более) в рельсах. Здесь обсуждаются самые ранние стадии деформации материала и образования трещин. Термин «зарождение трещины» неоднозначен, но инспекторы рельсов могут не принимать во внимание трещину с длиной поверхности менее 2 мм; это соответствует глубине трещины около 0,5 мм. Чтобы модель предсказывала срок службы рельса, необходимо понять, как накапливаются пластические деформации и повреждения, и как микроструктура влияет на образование и распространение трещин в этой области вблизи поверхности.
Ключевые слова: рельс, колесо, трещина, модель, исследование, цифровизация, рентген, изучение.
Введение. Реакция материала на циклическую нагрузку. Вобщем, материал, подвергающийся многократному нагружению, может реагировать четырьмя способами (рис. 1). Если циклическое напряжение меньше предела упругости материала, то реакция будет чисто упругой, а разрушение, если таковое имеется, произойдет из-за многоцикловой усталости. Если циклическое напряжение выше предела упругости, то будет иметь место некоторое пластическое течение, что приведет к образованию защитных остаточных напряжений, а также может вызвать деформационное упрочнение материала; если циклическое напряжение ниже «предела упругой приспособляемости», система будет приспособляться до состояния, в котором после нескольких циклов нагрузки реакция снова будет чисто упругой [1–10].
Рис. 1. Реакция материала на циклическую нагрузку
Если циклическое напряжение выше предела упругой приспособляемости, то система не будет приспособляться до чисто упругого состояния, и в каждом цикле будет происходить пластическая деформация. Для определенных циклов напряжения результирующая пластическая деформация может полностью измениться, и в конечном итоге вероятен отказ из-за малоцикловой усталости; такие замкнутые циклы пластической деформации возможны только ниже «предела пластической приспособляемости». Если цикл пластической деформации открытый, то после каждого цикла происходит чистое изменение пластической деформации. Направленное накопление пластической деформации называется «пластическим храповым механизмом», поэтому предел пластической приспособляемости также называют «порогом храпового механизма». В идеале система поезд-рельс и, в частности, материалы колеса и рельса должны быть спроектированы или выбраны таким образом, чтобы контакт колеса с рельсом проходил под напряжением ниже пределов упругой приспособляемости колеса и рельса.
Моделирование эволюции микроструктуры. Результаты. Направленное накопление пластической деформации изменяет микроструктуру материала рельса и колеса. Как правило, материал сильно деформируется в направлении напряжения сдвига в области контакта. очень близко к поверхности, нередки локальные деформации порядка 1000 %.
Результаты исследования с помощью рентгеновской аппаратуры (рентгенологическое исследование), компьютерной томографии большой (визуальной) трещины на изношенном рельсе, аналогичной показанной на рис. 2а, представлены на рис. 2 б.
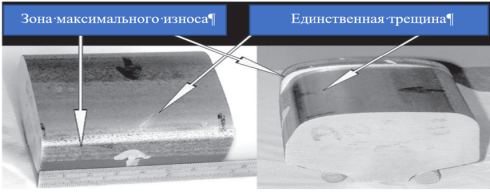
Рис. 2. Рентгенологическое исследование, компьютерная томография (б) трещины (а) на изношенном рельсе
Куб материала был извлечен вокруг трещины, а затем вращается перед сканированием, сфокусированным рентгеновским снимком. Трехмерное изображение было построено в цифровом виде (левое изображение на рис. 1б), которое затем можно «разрезать» в любой плоскости, чтобы исследовать особенности трещины.
Пластическая деформация упрочняет материал. Материал разрушается после накопления критической энергии деформации. Моделирование зарождения трещин и износа требует реалистичного представления микроструктуры материала рельса, подвергая его действию переходных контактных напряжений колесо-рельс, определяя пластическую деформацию и возможное деформационное упрочнение, модификацию микроструктуры при каждом проходе нагрузки. Этот процесс необходимо повторять в течение миллионов проходов колеса. по мере того, как материал деформируется, он портится и выходит из строя, образуя частицы износа и вызывая трещины.
Популярным метод создания реалистичных случайных микроструктур (поликристаллов) в 2D или 3D заключается в использовании метода [11–16]. Периодический «единичный куб» микроструктуры показан на рис. 3.
Рис. 3. Сгенерированный периодический «единичный куб» поликристаллической микроструктуры [11–14]
Изучали перлитную сталь с использованием этой методики. контактные напряжения, определенные с использованием предположения об изотропности, не являются точными при моделировании мезоскопического напряжения внутри зерна. Важным соображением является влияние анизотропии зерен и различной ориентации перлита между и даже внутри зерен.
Поперечное сечение деформируемого материала, параллельное направлению тяги и, следовательно, направлению максимальной деформации, моделируется в виде сетки прямоугольных элементов; свойства материала присваиваются индивидуально элементам шаблона, представляющего микроструктуру стали. Свойства феррита и перлита в рельсовой стали были определены с помощью измерений нанотвердости, а шестиугольная структура перлитных «зерен» на границах зерен легко создается и конфигурируется (рис. 4).
Рис. 4. Представление перлитной микроструктуры в виде гексагональных перлитных зерен, окруженных ферритом по границам зерен
Затем может быть применен ряд ортогональных распределений напряжения сдвига (либо 2D, как контакт двух дисков, либо 3D, как контакт колеса с рельсом), и смоделированная микроструктура накапливает пластическую деформацию сдвига до тех пор, пока элементы не достигнут предела своей пластичности и не начнут деформироваться до разрушения. Неисправные элементы на поверхности могут быть удалены как продукты износа; подповерхностные, они рассматриваются как места зарождения трещин или как материал, через который трещины будут распространяться быстро.
Вместо выводов. Направленное накопление пластической деформации сдвига проявляется в двух формах. В одном из краев контактной зоны выдавливаются тонкие полоски материала, что может привести, например, к «замятию» рельсов. Технически это износ, так как материал был удален из области контакта. При контакте колеса с рельсом номинальное контактное давление само по себе может быть достаточно большим, чтобы привести к храповику и вызвать рывки.
В другом варианте — пластическая деформация сдвига накапливается под поверхностью. На рис. 5 показаны трещины в поперечном сечении рельса, соответствующие деформации пластического сдвига. Накопление деформации пластического сдвига приводит к износу и возникновению трещин, приводящих к разрушению.
Рис. 5. СЭМ-изображение поперечного сечения рельса с двумя трещинами, способствующими пластическому срезу
Исследования изношенных рельсов и испытательных дисков (симуляция контакта рельсов) показали, что на возникновение и раннее распространение трещин сильно влияет микроструктура материала. В результате моделирования установлено, что распространение трещины зависит от поля напряжений. Необходимо отметить, что процессы раннего зарождения и распространения трещин не могут быть полностью смоделированы в двух измерениях, учитывая зернистый характер формирующейся и конечной микроструктуры.
Литература:
- Alwahdi, F., Franklin, F. J. and Kapoor, A. (2005), The effect of partial slip on the wearrate of rails, Wear, 258(7–8), 1031–37.
- Barber, C. B., Dobkin, D. P. and Huhdanpaa, H. T. (1996), The Quickhull algorithm for convex hulls, ACM Transactions on Mathematical Software, 22(4), 469–83, http:// www.qhull.org.
- Baumann, G., Fecht, H. J. and Liebelt, S. (1996), Formation of white-etching layers on rail treads, Wear, 191, 133–40.
- Beretta, S., Braghin, F., Bucca, G. and Desimone, H. (2005), Structural integrity analysis of a tram-way: load spectra and material damage, Wear, 258, 1255–64.
- Bower, A. F. and Johnson, K. L. (1991), Plastic flow and shakedown of the rail surface in repeated wheel–rail contact, Wear, 144, 1–18.
- Carroll R. I. and Beynon J. H. (2007a), Rolling contact fatigue of white etching layer: Part 1: Crack morphology, Wear, 262(9–10), 1253–66.
- Carroll R. I. and Beynon J. H. (2007b), Rolling contact fatigue of white etching layer: Part 2. Numerical results, Wear, 262(9–10), 1267–73.
- Clayton, P. and Su, X. (1996), Surface initiated fatigue of pearlitic and bainitic steels under water lubricated rolling/sliding contact, Wear, 200, 63–73.
- Desimone, H., Beretta, S. and Kapoor, A. (2005), Rail life prediction for tramcars under full slip regime, Proceedings 11th International Conference on Fracture, Turin, Italy, 20–25 March, available at: www.icf11.com/proceeding/EXTENDED/5422. pdf, accessed March 2009.
- Dyson, I. N., Williams, J. A. and Kapoor, A. (1999), The effect of surface hardening on the elastic shakedown of elliptical contacts, Proceedings of the IMechE: Part J, Journal of Engineering Tribology, 213, 287–98.
- Eden, H. C., Garnham, J. E. and Davis, C. L. (2005), Influential microstructural changes on rolling contact fatigue crack initiation in pearlitic rail steels, Materials Science and Technology, 21(6), 623–9.
- Ekberg, A. and Sotkovszki, P. (2001), Anisotropy and rolling contact fatigue of railway wheels, International Journal of Fatigue, 23, 29–43.
- Ertz, M. and Knothe, K. (2002), A comparison of analytical and numerical methods for the calculation of temperatures in wheel/rail contact, Wear, 253, 498–508.
- Fischer, F. D., Werner, E. and Yan, W.-Y. (1997), Thermal stresses for frictional contact in wheel-rail systems, Wear, 211, 156–63.
- Fleck, N. A., Kang, K. J. and Ashby M. F. (1994), The cyclic properties of engineering materials, Acta Metallurgy and Materials, 42, 365–81.
- Fletcher, D. I. and Beynon, J. H. (1998), The influence of lubricant type on rolling contact fatigue of pearlitic rail steel, in Dowson, D., Priest M., Taylor, A., Ehret, P.