Based on the studies, the following parameters were selected and described as control parameters for assessing the quality and efficiency of wellbore cleaning: well inclination, penetration rate, fluid and cuttings density, apparent viscosity of the fluid, penetration rate and rotation of the drill pipe. Their evaluation and ranges of application are given.
Keywords: wellbore cleaning, hole inclination, ROP, fluid density, cuttings density, fluid apparent viscosity, drill pipe rotation.
Wellbore cleaning is one of the main tasks in drilling oil and gas wells. When planning a well or drilling operations, one of the key parameters that must be determined is the minimum required flow rate to transport cuttings to the surface. A study by Amoco shows that 70 % of lost time due to unplanned events is caused by stuck drill pipe [6] and approximately one third of all stuck pipe problems are due to poor cuttings transport [4].
Based on the studies performed, the well inclination angle, penetration rate, density of fluid and cuttings, apparent viscosity of the fluid, rate of penetration and rotation of the drill pipe were selected as control parameters.
Well inclination angle. Studies have shown that the relationship between the angle of inclination of the well and the concentration of cuttings is not linear [5]. At angles of inclination less than 15°, the sludge concentration is slightly higher than in vertical cases; from 15 to 30°, the sludge concentration changes gradually as the angle of inclination increases; the range from 30 to 60° is «critical» for sludge transport, as the sludge concentration increases significantly; at angles of inclination from 60 to 90°, the formation of sludge layers is inevitable [8].
Density difference. Gravity is the main cause of cuttings settling. Thus, the difference between the density of the slurry and the density of the liquid plays a large role in the settling of the slurry, and the settling can be reduced if this gap is reduced. The density of cuttings observed when drilling oil and gas wells ranges from 2.4 to 2.82 g/cm3; at the same time, the density of drilling fluids mainly varies from 0.9 to 2.5 g/cm3. Thus, the density difference ranges from 0.6 to 1.9 g/cm3.
The Density Influence Factor is used to predict the sludge concentration at different sludge density or mud density. It can be obtained using the following equation:
When the density of the cuttings is equal to the density of the liquid, the cuttings slip rate becomes zero and cleanup is no longer a problem. However, such a scenario almost never occurs in practice while drilling.
Viscosity of a liquid. The effect of fluid viscosity on well cleanout depends on the angle of inclination of the well. Cuttings transport is a combination of weighing and carrying out in the wellbore. Liquids with high viscosity tend to gel within the sludge bed, resulting in difficulty in lifting the deposited sludge, causing high sludge concentrations. Low viscosity leads to insufficient particle shear, which also leads to high cuttings concentration in the wellbore [7].
In wells with small angles of inclination, suspension prevails in the process of cuttings transfer and liquids with high viscosity work somewhat better [8]. In high slope areas, cuttings tend to be deposited on the bottom wall of the annulus. High viscosity reduces the fluid velocity in the near-wall region and increases the strength of the cuttings layer [3, 7].
Thus, gel strength, consistency index and liquid behavior index affect the concentration of the slurry. In laboratory experiments, a viscometer reading of 100 rpm is commonly used because the shear rate at this rotational speed best reflects the shear rate that is observed in the annulus during drilling [2].
Based on this criterion, drilling fluids are divided into three categories: low viscosity fluids (
Penetration speed. There is an almost linear relationship between ROP and cuttings concentration in the wellbore [5]. The penetration rate range (from 10 to 45 m/h) is acceptable for practical use. Based on the authors' experience from pilot testing, this approach is not recommended for cases with ROP above 75 m/h or less than 3 m/h.
Drill pipe rotation. The effect of drill pipe rotation on cuttings concentration depends on the angle of inclination of the wellbore. In highly deviated wells, the rotation of the drill pipe tangentially oscillates the cuttings layer and shakes the cuttings from the bottom of the annulus, which facilitates the removal of the cuttings by a high-velocity fluid flow to the top of the annulus. At medium inclination angles, cuttings also tend to be deposited on the bottom wall of the annulus. Since the angle of inclination in this position is smaller than in the strongly inclined part, the amount of precipitation (caused mainly by gravity) is less. Cuttings are easier to carry to the top, so the effect of drill pipe rotation in this area is negligible. In nearly vertical wells, the effect of drill pipe rotation on cuttings concentration is negligible.
The author [1] investigated the effect of drill pipe rotation on cuttings transport by conducting a series of experimental tests on an 8" x 4.5" x 90 ft flow loop. In this article, the effect of drill pipe rotation is considered using the drill string rotation factor (DEF). DEF is obtained with the correlations proposed by [1] for 0.08 inches. sludge, as shown in Fig. 1.
The influence of drill pipe rotation depends on the angle of inclination, fluid properties, rotation speed and cuttings dimensions. However, the most important role is played by the speed of rotation of drill pipes and the angle of inclination of the well [1]. Fig. 1. is based on light thin liquid data.
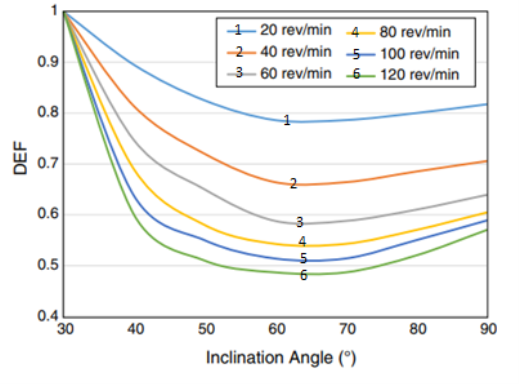
Fig. 1. Graph of the effect of rotation of the drill pipe [1]
Conclusion . Thus, it can be argued that the most unfavorable part for ERD wellbore cleanup is between 45 and 55°. If the well cleanout requirement is met for this part, it should not be a problem for other parts of the well. Since the cuttings slide down when flow decreases in this area, the pump should not be stopped until all the cuttings have been removed to prevent clogging of the wellbore.
The results were confirmed [8] by geometry data with a diameter ratio of 1 to 2.5 (borehole diameter/pipe diameter).
For conditions with very large diameter ratios (e.g., coiled tubing drilling) and very small diameter ratios (eg, casing drilling), the results can be significantly skewed. This method may also not work for very small cuttings (less than 1 mm) and large cuttings (> 5 mm).
In addition, this method cannot be used in situations with very high cuttings concentration (more than 40 %), such as low fluid velocity (less than 0.61 m/s) and high ROP (more than 75 m/h).
References:
- Bassal, A. A. 1996. The Effect of Drillpipe Rotation on Cuttings Transport in Inclined Wellbores. MS thesis, The University of Tulsa, Tulsa, Oklahoma (May 1996).
- Bourgoyne, A. T., Millheim, K. K., Chenevert, M. E. et al. 1986. Applied Drilling Engineering, 113–189. Richardson, Texas: SPE.
- Hashemian, Y., Yu, M., Miska, S. et al. 2014. Accurate Predictions of Velocity Profiles and Frictional Pressure Losses in Annular YPL-Fluid Flow. J Can Pet Technol 53 (6). SPE-173181-PA. http://dx.doi.org/ 10.2118/173181-PA.
- Hopkins, C. J. and Leicksenring, R. A. 1995. Reducing the Risk of Stuck Pipe in the Netherlands. Presented at the SPE IADC Drilling Conference, Amsterdam, 29 February-2 March. SPE-29422-MS. http:// dx.doi.org/10.2118/29422-MS.
- Larsen, T. F. 1990. A Study of the Critical Fluid Velocity in Cuttings Transport for Inclined Wellbores. MS thesis, The University of Tulsa, Tulsa, Oklahoma.
- Massie, G. W., Castle-Smith, J., Lee, J. W. et al. 1995. Amoco’s Training Initiative Reduces Wellsite Drilling Problems. Pet. Eng. Inti. 67 (3). United States, http://www.osti.gov/scitech/biblio/39900.
- Saasen, A. et al. 2002. The Effect of Drilling Fluid Rheological Properties on Hole Cleaning. Presented at the IADC/SPE Drilling Conference, Dallas, 26–28 February. SPE-74558-MS. http:// dx.doi.org/10.2118/74558-MS.
- Zhang, F., Miska, S., Yu, M., Ozbayoglu, E., & Takach, N. (2017). A Fast Graphic Approach to Estimate Hole Cleaning for Directional Drilling. SPE Drilling & Completion, 32(01), 51–58. doi:10.2118/173681-pa