Для достижения конкурентоспособности радиоэлектронной аппаратуры необходимо уделить особое внимание обеспечению высокого качества и повышению надежности на всех этапах производства. В статье представлены и классифицированы основные дефекты, возникающие на стадии изготовления электронной аппаратуры. Описаны современные методы автоматизированного контроля качества монтажа электронных устройств. Рассмотрено пересечение множеств дефектов и средств контроля, а также предложен оптимальный метод контроля.
Ключевые слова: дефект, методы контроля, автоматическая оптическая инспекция, неразрушающий рентгеновский контроль.
В условиях активного развития производства радиоэлектронных устройств и функциональных узлов, изготавливаемых автоматизированными или ручными методами монтажа, промышленность предъявляет высокие требования к их качеству. Эти требования основаны на сложности сборки и необходимости быть конкурентоспособными на современном рынке.
На сегодняшний день существует острая потребность в ряде изделий радиоэлектронной промышленности «старого образца». Большинство из которых изготавливается ручными методами монтажа компонентов на печатные платы. [1]
Каждый изготовленный электронный модуль проходит через операцию визуального контроля ОТК. По статистике при таком контроле обнаруживается не более 75 % от общего числа дефектов, которые возможно обнаружить визуальными методами контроля. В условиях сокращения времени выполнения операций монтажа, спешки исполнителей и недостаточной квалификации новых работников, количество дефектов значительно увеличивается. Не обнаруженные на стадии визуального контроля дефекты могут привести к отказам дорогостоящих компонентов на этапе функциональной проверки.
Таким образом существует острая необходимость в применении автоматизированного контроля монтажа изделий радиоэлектронной промышленности.
Классификация дефектов
Все дефекты радиоэлектронных устройств можно разделить на три категории:
- дефекты компонентов — это дефекты, которые возникают при операциях монтажа (установке, заготовке, монтировании элементов или проводников на печатную плату, склеивании) радиоэлектронных устройств;
- дефекты паянных соединений — это дефекты, которые возникают только в структуре припоя при операции пайки; [2]
- дефекты печатных плат.
Основные дефекты монтажа электронных устройств, возникающие при различных способах пайки, можно классифицировать следующим образом:
- Шарики припоя — это сферические образования из припоя, оставшиеся после пайки, которые разбрасываются вокруг паяного соединения при его оплавлении в процессе пайки. К ним также относятся брызги припоя.
- Отсутствие паянного соединения: не оплавленная паяльная паста, которая после процесса пайки остается в виде массы, состоящей из отдельных шариков припоя, отсутствие контакта отдельных выводов компонентов с оплавленным припоем, вывод компонента приподнят над галтелью припоя, эффект «надгробного камня».
- Неверный номинал элемента — установка элемента в том же корпусе, но другого номинала, допусков отклонений, мощности и тд.
- Отсутствие элемента — элемент не установлен согласно электрической схеме.
- Установка элемента не по электрической схеме — элемент установлен на соседнюю площадку (отверстие), либо перепутана полярность элемента при установке.
- Отсутствие электрической связи с компонентом — не припаян вывод компонента.
- Повреждения компонентов — сколы и трещины, обнаруженные после операции пайки, которые могут возникать, как в результате неправильного выбора температурных профилей пайки, так и на последующих операциях, например, при испытаниях на вибрацию, удары или воздействие термоциклов.
Дефекты паянных соединений
Качество паяных изделий определяется их прочностью, работоспособностью, надежностью, коррозионной стойкостью и способностью выполнять специальные функции, такие как теплопроводность, электропроводность и коммутационные характеристики. Чтобы обеспечить эти характеристики, необходимо принять оптимальные решения в процессе производства паяного изделия.
К наиболее распространенным недостаткам паяных соединений относят: поры, раковины, включения шлака и флюса, непропаи и трещины. Эти дефекты можно разделить на две группы: первая связана с неправильным наполнением расплавом припоя зазоров между соединенными элементами, а вторая возникает в процессе охлаждения после пайки. Дефекты первой группы обусловлены особенностями заполнения капиллярных зазоров во время пайки. Дефекты второй группы возникают из-за уменьшения растворимости газов в металлах при их переходе из жидкого состояния в твердое, а также из-за усадочных явлений. Эту группу также составляют пористость, вызванная кристаллизацией и диффузией. Кроме того, к дефектам прочности относятся трещины, которые могут появиться в металле шва, в области пайки или в паяемом металле. Отдельную категорию дефектов составляют включения шлака и флюса.
Неправильное конструирование паяного соединения, наличие замкнутых полостей, блокирование газа при неравномерном нагреве или зазоре, а также недостаточное смачивание поверхности паяемого металла — все это является причинами образования непропаев у границы раздела с паяемым металлом. Также блокированные остатки газа в швах могут возникать из-за неравномерности движения фронта жидкости при затекании припоя в зазор. Это приводит к раздроблению фронта на участки с разными скоростями продвижения, что может привести к отделению небольших объемов газа. Таким же образом захват флюса и шлаков может происходить в шве.
Дефекты печатных плат
Дефекты печатных плат делятся на два вида: видимые и скрытые.
К дефектам печатных плат, которые можно заметить внешним осмотром или измерениями, относятся трещины, царапины, вмятины и сколы, а также нарушение диэлектрической основы: скручивание или изгибы. [3]
Скрытые дефекты возникают в результате нарушения производственных технологий или использования низкокачественных материалов. Они могут быть обнаружены только при помощи специализированного оборудования или в процессе эксплуатации. Многослойные платы чаще всего страдают от подобных дефектов.
Методы контроля
С целью увеличения количества годных изделий на каждом этапе монтажа, необходимо в процесс включать операции контроля качества.
Выбор метода или комплекса методов контроля для обнаружения дефектов паяных соединений следует проводить в соответствии с требованиями, предъявляемыми к качеству паяных соединений стандартами, техническими условиями и чертежами, утвержденными в установленном порядке, и с учетом размеров фактически выявляемых дефектов и производительности методов контроля. [4]
Для определения необходимого метода контроля необходимо разделить дефекты на несколько подкатегорий по способу обнаружения: определяемые визуально (бесконтактные) и определяемые объективно при помощи измерения электрических параметров (контактные). [8]
Таблица 1
Бесконтактные методы обнаружения дефектов .
Вид контроля |
Описание метода |
Визуальное наблюдение объекта человеком |
Наблюдение за объектом визуально |
Фотооптический контроль |
Анализ фотоснимков изделия с необходимым разрешением |
Видеооптический контроль |
Анализ видеофайла с записью движения объектива вокруг изделия |
3Д модель объекта |
Анализ 3Д модели изделия, выполненного с помощью 3Д-сканера |
Рентгенография |
Анализ рентгеновского снимка |
Тепловой снимок |
Анализ отклонения градиента температуры на тепловом снимке |
Таблица 2
Контактные методы обнаружения дефектов.
Вид контроля |
Описание метода |
Функциональный контроль через интерфейсы |
Проверка соответствия выходных и промежуточных параметров цепей, логических компонентов, «вшитых» настроек через интерфейсы (разъёмы) |
Функциональный или параметрический контроль при помощи «ложе гвоздей» |
Проверка соответствия выходных и промежуточных параметров цепей, логических компонентов, «вшитых» настроек через точки контакта на плате |
Метод «Летающие зонды (щупы)» |
Проверка соответствия промежуточных параметров цепей и логических компонентов |
Метод «Летающие матрицы» |
Проверка соответствия промежуточных параметров цепей и логических компонентов |
Одними из наиболее распространенных методов контроля качества электронных компонентов являются оптический и рентгеновский неразрушающий контроль. Автоматическая оптическая инспекция (АОИ) позволяет обнаружить поверхностные дефекты компонентов и конфигурации электронных сборок, а также дефекты паянного соединения.
На сегодняшний день многие компании поставщики оборудования для оптического контроля монтажа предлагают роботизированные системы. Это комбинация робота и оптического инспекционного модуля, позволяющее осуществлять широкий спектр инспекционных задач. Шестиосевой манипулятор и динамическая система подсветки обеспечивают гибкое перемещение инспекционного модуля и получение контрастного изображения под углами от 0° до 90°. Датчики измеряют толщину влагозащитного покрытия и высоту установки компонентов.
Рис. 1. Роботизированная система оптического контроля «Комплекс FLEX» компании Ostec
С целью обнаружения скрытых дефектов используется неразрушающий рентгеновский контроль (НРК). Принцип такого метода заключается в следующем: рентгеновские лучи проникают в компоненты печатной платы и затухают, проходя через различные материалы. На выходе получится снимок с яркими и темными областями.
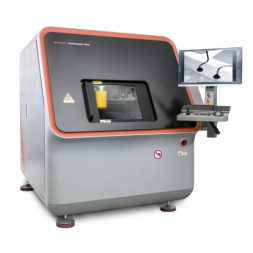
Рис. 2. Пример оборудования для рентген-контроля печатных плат
При измерении электрофизических параметров тесты проводят по двум направлениям: проверка электрофизических параметров и проверка исправности циклограммы работы платы. Одним из основных методов параметрического контроля (ПК) является метод «летающие щупы». Оборудование для метода летающих щупов имеет несколько подвижных головок, на каждой из которых установлен щуп с приводом по оси. Щупы по заранее созданной оператором программе контактируют с платой, в результате чего происходит подача питаний, сигналов и производятся измерения. [7]
Рис. 3. Пример параметрического контроля с применением метода «летающие щупы»
Существую также методы контроля функциональных характеристик электронных устройств. Для этого используются узкоспециализированная стендовая аппаратура, средства измерения и испытательное оборудование. Функциональная проверка электронной аппаратуры, осуществляемая при помощи измерения электрических параметров, позволяет полностью проверить характеристики электронных устройств. Но при проверке необходима подача питающих напряжений на входные цепи. При наличии некоторых видов дефектов это может привести к выходу из строя дорогостоящих компонентов, например, в результате замыкания или неправильной установки элемента в процессе монтажа. Во избежание повреждения компонентов цепей электронных устройств необходима предварительная проверка до подачи питающих напряжений.
Таблица 3
Возможности АОИ, НРК и ПК по обнаружения и локализации различных видов дефектов. [5] [6]
Виды дефектов |
АОИ |
НРК |
ПК |
Дефекты компонентов |
|||
Смещение компонента (с сохранением контакта) |
+ |
+ |
- |
Смещение компонента (без сохранения контакта) |
+ |
+ |
+ |
Отсутствие компонента |
+ |
+ |
+ |
Неверная полярность компонента |
+ |
- |
+ |
Неверный номинал элемента |
+ |
- |
+ |
Повреждение компонента (царапины, сколы) |
+ |
- |
- |
Отсутствие электрической связи с компонентом |
+/- |
+ |
+ |
Не припаян вывод компонента (при наличии контакта) |
+ |
+ |
- |
Дефекты паянного соединения |
|||
Недостаток припоя |
+ |
+ |
- |
Брызги (шарики) припоя |
+ |
+ |
- |
Замыкание (мостики припоя) |
+ |
+ |
+ |
«Холодная» пайка |
+ |
+ |
- |
Трещина (повреждение) соединения |
+ |
+ |
+/- |
Не пропаянное соединение |
+/- |
+ |
+ |
Пустоты |
+/- |
+ |
- |
Дефекты печатной платы |
|||
Нарушение металлизации переходных отверстий |
- |
+ |
+/- |
Обрыв проводника (внутренний слой) |
- |
+ |
+ |
Замыкание проводника (внутренний слой) |
- |
+ |
+ |
Отслоение проводника от диэлектрика |
+/- |
+ |
- |
Согласно статистическим данным за 3 года на одном из предприятий, выпускающем радиоэлектронные устройства, ОТК было проверено около 15500 электронных узлов на печатных платах. При проверке обнаружено 322 дефекта. Из них 206 — дефекты паянных соединений (64 %), 114 — дефекты компонентов (35,4 %) и 2 — дефекты печатной платы (0,6 %).
Выводы
По результатам классификации всевозможных видов дефектов, возникающих в радиоэлектронных узлах, и анализа наиболее распространённых на сегодняшний день методов и средств автоматизированного контроля получено пересечение множеств дефектов и средств контроля (Таблица 3). С учетом статистических данных можно предположить, что наиболее оптимальным будет выбор оборудования для обнаружения дефектов с помощью автоматической оптической инспекции. Данный метод позволит обнаружить до 99 % дефектов. С целью обнаружения всех возможных видов дефектов целесообразно совместное использование оптического и рентгеновского контроля.
Литература:
- ГОСТ Р МЭК 61191–1–2010 Национальный стандарт Российской Федерации. Печатные узлы Часть 1. Поверхностный монтаж и связанные с ним технологии. Общие технические требования. 39 с.
- ГОСТ 19249–73. Соединения паяные. Основные типы и параметры. 13 с.
- ГОСТ Р 53386–2009. Платы печатные. Термины и определения. 15 с.
- ГОСТ 24715–81. Соединения паяные. Методы контроля качества. 9 с.
- Калинченко Н. П., Викторова М. О., 2012. Атлас дефектов паяных соединений: учебное пособие. Томск: Издательство Томского политехнического университета. 83 с.
- Осипенко А. А., Игнатенкова О. А., Григоров М. С., Басов О. О. Обоснование необходимости совместного применения автоматической оптической инспекции и неразрушающего рентгеновского контроля электронных модулей // Научный результат. Информационные технологии. — Т.2, № 2, 2017. 6 с.
- Функциональное тестирование печатной платы URL: https://habr.com/ru/companies/thirdpin/articles/425569/
- Контроль качества печатных плат URL: https://zctc.ru/sections/kontrol_kachestwa_pechatnih_plat