В современном мире анализ и изучение физических объектов с помощью цифровых технологий имеют высокую актуальность из-за относительной дешевизны и простоты процесса. Одним из ключевых направлений использования цифровых технологий в сфере нефтехимической промышленности является оптимизация процесса с ключевыми задачами, как увеличение выхода целевого продукта, снижение энергетических затрат процесса на реальных установках. Модели, созданные при помощи цифровых технологий, называют цифровыми двойниками. Их главным преимуществом является возможность предсказывать результаты процесса, основываясь на собранной базе данных, которая, в свою очередь, должна иметь большое количество качественных данных. Для этого необходимо также её анализировать и выделять аномальные параметры, которые с реальностью не имеют ничего общего. С большим количеством информации человеку необходимо большое количество времени на анализ таких баз данных. В таком случае люди для ускорения процесса анализа применяют нейронные сети, которые способны проанализировать базу данных и выделить аномальные значения в считанные секунды. В данной работе рассматривается процесс создания цифрового двойника колонны фракционирования с применением нейронных сетей.
Ключевые слова: цифровые технологии, цифровые двойники, нейронные сети, обучение нейронных сетей.
Цифровой двойник, как можно понять из названия, это цифровая или виртуальная модель реального объекта, система или процесса, которая полностью отвечает своим реальным прототипам при помощи систем математических уравнений и зависимостей [1]. Такие модели создаются с целью исследования объекта в различных условиях для анализа возможных последствий, для оптимизации процесса или для предотвращения нежелательных случаев. В наше время цифровые двойники имеют очень высокую востребованность во многих сферах деятельности, так как при их помощи на основе имеющейся информации можно предсказывать, так как у них имеется множество различных применений, которые ещё не были упомянуты. В нефтяной промышленности цифровые двойники имеют множество применений: поиск нефтяных месторождений [2], обучение специалистов в различных сценариях [3], анализ и оптимизация существующего оборудования [4] и т. д. На основе цифровых двойников не только оптимизируют уже существующие объекты, но также создают новые с учетом опыта эксплуатации похожих объектов. Таким образом, компании не только экономят на построении модели объекта, но и экономят время на реализации самого проекта.
В нашей работе мы воссоздали модель колонны фракционирования на установке риформинга. Сырьем колонны является стабильный риформат после процесса риформинга. Продуктами колонны являются газ остаточных легких углеводородов, который направляется на факел, фракции от начала кипения (НК) до 62 °С, который применяется в качестве компонента товарного бензина в торгово-сервисных центрах (ТСЦ), фракции от 62 до 90 °С, который применяется как сырье промышленных установок для получения ароматических углеводородов и как компонент товарного бензина в ТСЦ, и фракции от 90 °С до конца кипения (КК), которые имеют такое же применение, как фракции 62–90 °С. Целевым продуктом являются фракции 90-КК °С, поэтому в нашей работе будет выполняться анализ с целью увеличения выхода именно этого продукта.
В качестве исходных данных был взят регламент установки риформинга, режимные листы и нормы технологического режима работы установки.
Методику создания цифрового двойника представим на рисунке 1.
Рис. 1. Методика создания цифрового двойника
Далее по пунктам представим процесс создания цифрового двойника:
- Как было сказано ранее, за основу модели был взят регламент установки риформинга и его режимные листы. Но нам не был неизвестен состав и свойства сырья колонны фракционирования, поэтому было предпринято решение воссоздать модель установки риформинга вплоть до колонны фракционирования. В качестве среды моделирования была взята программа UniSim Design, термодинамический пакет — «Peng-Robinson». В качестве сырья установки создавалась проба нефти по режимным листам с учетом содержания различных примесей. На протяжении воссоздания модели, многие элементы задавались строго по регламенту, чтобы получить наиболее реалистичные состав и свойства сырья колонны фракционирования.
- После создания модели была выполнена оценка адекватности модели. В результате, все параметры и условия процесса были выполнены в допустимых значениях регламента и соответствовали значениям из режимного листа с учетом погрешности в 5 %. После того, как мы убедились в адекватности модели, с целью оптимизации и ускорения процесса сбора данных, было решено из всей модели оставить только сырье колонны фракционирования и саму колонну непосредственно. Представим полученную модель на рисунке 2.
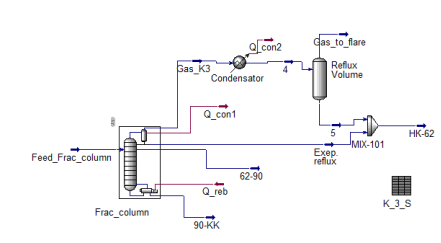
Рис. 2. Модель колонны фракционирования
- Для сбора данных был написан алгоритм на базе языка программирования Python с использованием таких библиотек, как numpy — для создания массивов, в которые будут записываться значения из среды моделирования при переборе переменных, и csv — для создания удобной базы данных в виде таблицы в формате.csv. На рисунке 3 представлен алгоритм процесса создания базы данных в виде блок-схемы.
Рис. 3. Блок-схема алгоритма процесса сбора базы данных
- Собранная база данных на данный момент состоит из 13781 строчек и 13 рядов, в которые было записаны температурный режим колонны, объемные и массовые расходы потоков, а также нагрузки на ребойлер и конденсатор. Также, на данный момент анализ проводился при статичном массовом расходе сырья колонны фракционирования, а также температуры орошения. В будущем предполагается расширение базы данных с учетом варьирования этих двух параметров, чтобы получить наиболее полный цифровой двойник колонны фракционирования.
Для анализа данных помимо ранее озвученных библиотек была выбрана scikit-learn — простая и эффективная библиотека для машинного обучения и предиктивного анализа данных. Она применяется в различных целях, основными выделяют классификацию и регрессия. Библиотека scikit-learn предлагает нам большое количество различных методов обучения, которые применяются при разных условиях анализа данных, а также в зависимости от выбранного метода будет разниться и точность предсказаний нейронной сети.
Предварительно перед обучением нейронной сети при помощи библиотеки seaborn визуализируем значения базы данных для того, чтобы выделить аномальные значения, которые могут послужить ухудшением точности предсказаний нашей нейронной сети. На рисунке 4 представим график зависимости объемного расхода фракций 90-КК °С от нагрузки ребойлера:
Рис. 4. Зависимость объемного расхода фракций 90-КК °С от нагрузки ребойлера
Как мы видим, база данных имеет несколько аномальных результатов, которые сильно отличаются от большинства. Такие желательно из базы данных удалять с целью повышения качества и точности нейронной сети. Это можно сделать как вручную, к примеру, при помощи офисного приложения Microsoft Excel, который способен в своей среде представлять данные.csv формата. Но если мы имеем дело с большим массивом данных, то вручную это делать очень долго, поэтому более оптимальным методом является непосредственное использования отдельного программного кода, при помощи которого можно будет находить и удалять подобные аномалии.
После всех вышеуказанных действий, был создан алгоритм обучения нейронной сети. В качестве методов обучения были использованы: LinearRegression — который соответствует линейной модели с коэффициентами, RandomForestRegressor — который подбирает ряд регрессоров дерева решений для различных подвыборок набора данных и GradientBoostingRegressor — который строит аддитивную модель поэтапно [5]. Несколько методов обучения были взяты с целью выяснить, какой метод для нас наиболее подходящий. Для обучения нейронной сети были созданы два массива — X и у. В массив X мы включим задаваемые нами параметры — температурный режим колонны и желаемый получаемый объемный расход фракций 90-КК °С. В будущем предполагается заменить задаваемый объемный расход фракций 90-КК °С на значение массового расхода сырьевого потока колонны фракционирования. В массив y были добавлены все остальные ряды базы данных.
В результате обучения нейронной сети, мы выполнили оценку точности её предиктивных способностей:
– LinearRegression: 61,1 % точности;
– RandomForestRegressor: 73,5 % точности;
– GradientBoostingRegressor: 74,8 % Точности.
Как мы видим, предположительно, наиболее точным на данный момент является метод GradientBoostingRegressor. Чтобы убедиться в этом, было выполнено сравнение результатов, полученные в среде моделирования UniSim Design с результатами предсказаний всех трех нейронных сетей.
К примеру, возьмем следующие параметры:
– Температура верха: 67,32 °С;
– Температура бокового отбора: 97,52 °С;
– Температура ребойлера: 150,1 °С;
– Предположительный объемный расход нижнего продукта: 56 м 3 /ч
Результаты представим в таблице 1.
Таблица 1
Сравнение результатов предсказания с моделью
Температура сырья, °С |
Об. расход НК-62, м 3 /ч |
Об. расход 62–90, м 3 / ч |
Масс. расход газа, кг/ч |
Масс. расход НК-62, кг/ч |
Масс. расход 62–90, кг / ч |
Масс. расход 90-КК, кг/ч |
Нагрузка конд., ккал / ч |
Нагрузка реб., ккал / ч |
|
UniSim Design |
120 |
2,12 |
2,99 |
0 |
1386 |
1962 |
40652 |
805765 |
1352229 |
LR |
114 |
3,67 |
2,97 |
550 |
1365 |
1969 |
40636 |
778472 |
1458789 |
RFR |
117 |
2,17 |
3,05 |
0 |
1351 |
2019 |
40630 |
750372 |
1392300 |
GBR |
115 |
3,87 |
3,02 |
245 |
1284 |
1963 |
40627 |
736478 |
1393426 |
Как мы можем наблюдать, наиболее близкие результаты были получены при помощи метода обучения RandomForestRegressor.
Вывод: На данный момент создан цифровой двойник типа цифровая тень, то есть такой цифровой двойник может с определенной точностью предсказывать результаты только в рамках представленной базы данных. Для расширения предиктивных способностей цифрового двойника будет расширение существующей базы данных с учетом разной подачи сырья в колонну фракционирования и разной температуры орошения.
Литература:
- Что такое цифровой двойник [Электронный ресурс] — URL: https://trends.rbc.ru/trends/industry/6107e5339a79478125166eeb (Дата обращения 17.03.2024).
- Азиева, Р. Х. Экономические аспекты внедрения цифровых технологий в современную геологоразведку / Р. Х. Азиева, Т. В. Якубов. — Текст: непосредственный // Инженерные и информационные технологии, экономика и менеджмент в промышленности. — Волгоград: Сборник научных статей, 2020. — С. 7–13.
- Волкова, М. М. Применение виртуальных тренажеров для обучения специалистов нефтегазовой отрасли / М. М. Волкова, Р. А. Манурова, Д. Н. Шайдуллина. — Текст: непосредственный // Вестник технологического университета. — 2019. — № Т.22, № 4. — С. 115–121.
- Fei Shen, Shuang Shuang Ren, Xiang Yang Zhang, Hong Wu Luo, Chao Min Feng, «A Digital Twin-Based Approach for Optimization and Prediction of Oil and Gas Production», Mathematical Problems in Engineering, vol. 2021, Article ID 3062841, 8 pages, 2021. https://doi.org/10.1155/2021/3062841.
- scikit-learn [Электронный ресурс] — URL: https://scikit-learn.org/stable/index.html (Дата обращения: 17.03.2024).